Without inertial sensors, modern rail transport would be inconceivable.
Inertial sensors perform numerous important tasks in the development and operation of trains. One of them is high-precision measurement of oscillations and vibrations on rolling stock, tracks and bridges. The data obtained from these measurements form the basis for safe, comfortable rail transport. Engineers can draw valuable information from them for train design and infrastructure maintenance. Sensors also ensure that the train dispatchers at the railway control centres – such as with our client Deutsche Bahn – always know the exact location of any given train. Satellite navigation alone is not enough because the signals are susceptible to interference.
ASC is specialised in measurement technology and manufactures a wide range of highly sensitive accelerometers and gyroscopes, as well as Inertial Measurement Units (IMU) for rail transport testing and monitoring. The sensors collect data in a wide variety of applications – not only in rolling stock, but also on tracks.
Fatigue Strength Testing under Extreme Conditions
Capacitive accelerometers from ASC do many things, including making trains safer. Rolling stock manufacturer Alstom uses them to measure the running dynamics (as per EN 14363) and the bogie strength (as per EN 13749) under real-life conditions. The ASC sensors used for this purpose not only have a high signal amplitude of ±2.7V for measurement ranges from ±2–200g, but also a wide DC frequency range of up to 7kHz. They also have high long-term stability, enabling accurate measurement of even low linear accelerations and low-frequency, dynamic and static constant accelerations. The sensors are extremely robust to weather conditions, withstand shocks of an intensity of up to 6,000g and operate in a temperature range between -40°C (-40°F) and +125°C (257°F). These are important prerequisites for use on test tracks, as the measurement technology is exposed to all kinds of weather on them.
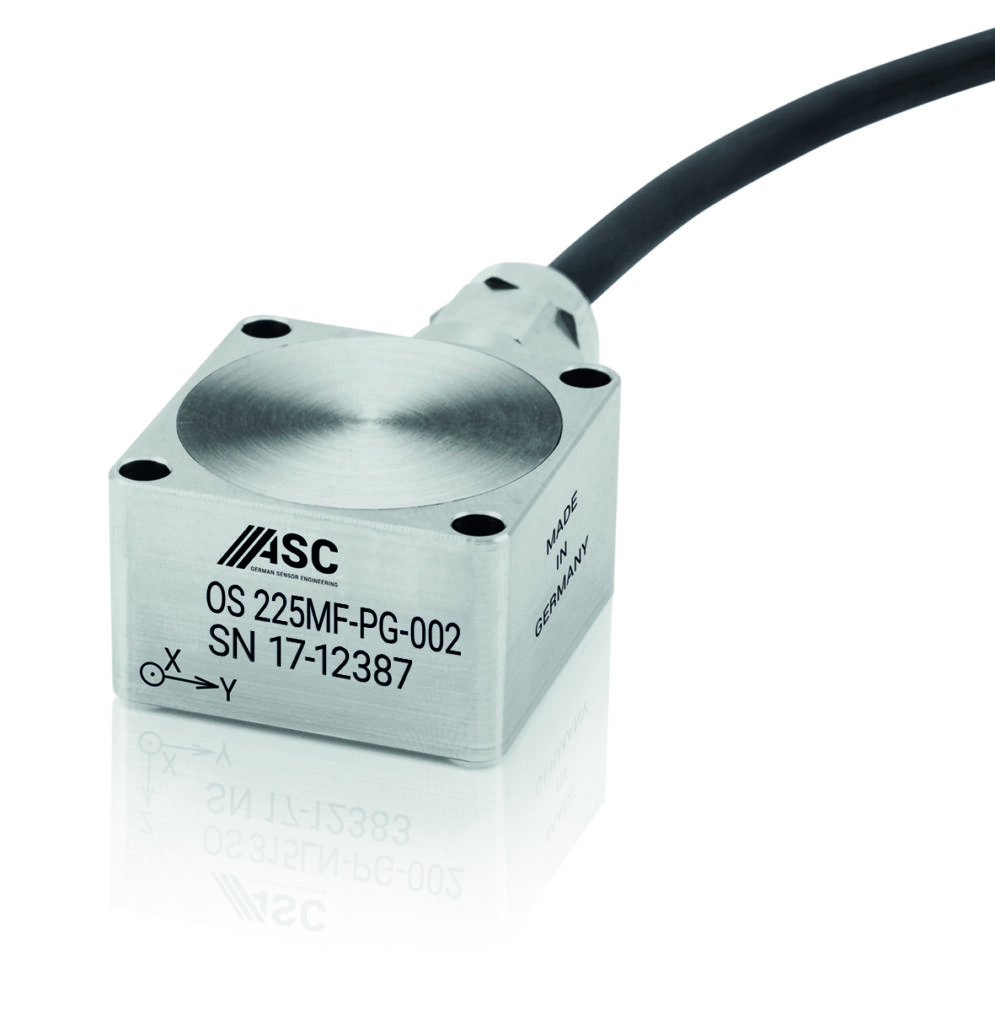
Bridging Navigation for Interrupted GNSS Signals
Sensors also play an important role in the exact positioning of trains, since knowing exactly where they are is vital for rail safety. Satellite navigation alone is not enough, as GNSS signals are lost in tunnels, forest areas or covered railway stations, with no or only very weak reception. Inertial Measurement Units from ASC take over position determination in these areas, thus bridging the time taken for the satellite signal to be fully available again. IMUs are ideal for this field of application because they capture even the slightest rotatory and linear movements and take up very little space.
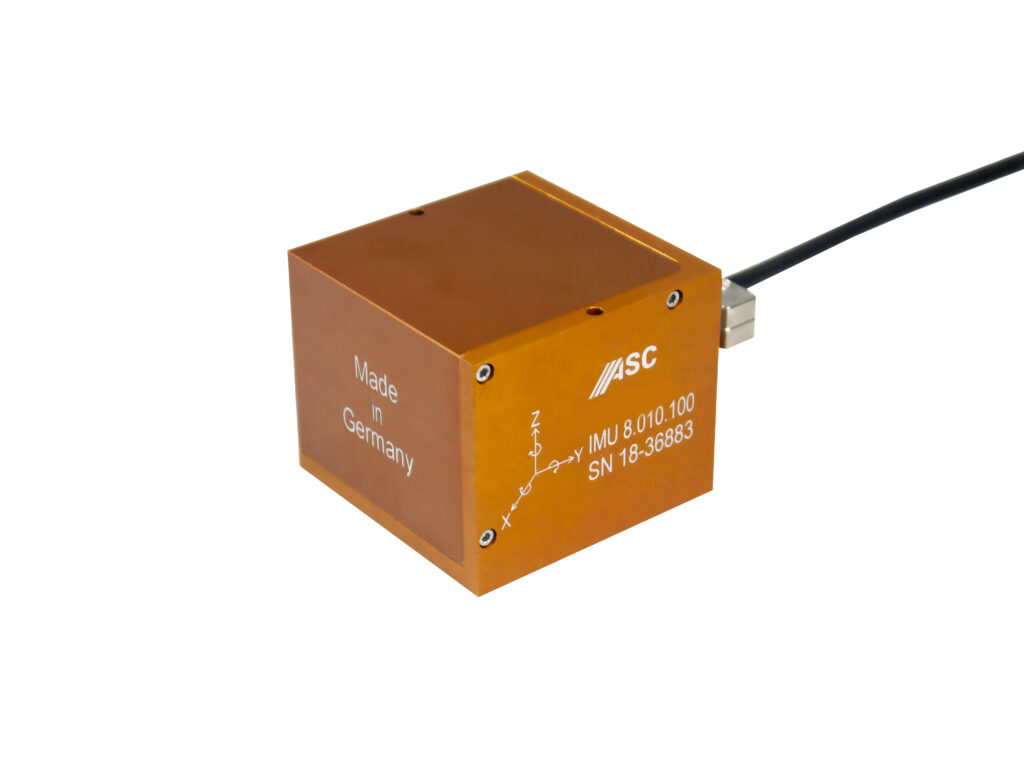
Case Study: The SAMIRA Research Project
ASC Inertial Measurement Units are used to determine, for example, the position of freight cars in Aachen University of Applied Sciences’ SAMIRA research project. This project involves the development of a smart rear-view camera to make freight trains’ switching process significantly more efficient. The camera, together with sensors, monitors the car’s travel, and thus requires less personnel. This will help to overcome the skills shortage which also prevails in rail transport and improve the overall competitiveness of rail freight. The ASC IMU is used as a backup for position determination on freight cars. It captures the exact position of the cars, even if the satellite navigation signal is temporarily interrupted. This guarantees the continuous high-precision localisation of the cars so that switching operations can be carried out much faster in the future.
Track Damage Detected Early
Capacitive and piezoelectric accelerometers are also essential for continuous track monitoring (CTM). Deutsche Bahn AG has been using ASC sensors for track data acquisition on its long-distance trains for several years, with the sensors in normal operation measuring the vertical acceleration in the wheelset bearings and the acceleration inside the car bodies (as per EN 13848).
DB Systemtechnik GmbH – Deutsche Bahn’s engineering office – can use the data obtained to identify irregularities in the longitudinal level of the track structure. Variations in longitudinal level have a major impact on performance levels. If there are errors in the geometry, maintenance measures must be taken immediately. In extreme cases, whole sections of track may even have to be closed. CTM using sensors allows potential damage to be detected and remedied at an early stage. This has absolutely no adverse effect on vehicle operation.
Functional Modules System for Maximum Flexibility
With the volume of rail passengers constantly growing, this leads in turn to an increasing burden on the network and the trains. Digital technologies are used more and more in the railway sector to meet these high demands. They require ever more compact and intelligent sensor solutions. With its smart sensors and functional module system, ASC can meet these challenges. The functional module system comprises, firstly, the hardware used, consisting of reliable and proven sensor elements for determining the physical values of acceleration and/or angular velocity, the housing suited to the harsh environment conditions and the wired or wireless data transmission with a variety of standardised interfaces. Secondly, it includes the flexible combinable software components for signal processing, which is done locally on the sensor itself.
ASC’s Smart Sensors have computing power that can be freely used to customise the characteristic extraction algorithms to suit your needs. Pre-processing performs data reduction in the first stage of the process. On this basis, for example, fast Fourier transforms (FFTs), wavelets or time series characteristic vectors can be extracted. The subsequent trend analysis and/or clustering of the results thus generates targeted status information about the components or the system. Users are always responsible for their own data sovereignty and application programming interfaces (APIs) are used to integrate customer-specific algorithms.
Smart inertial sensors from ASC can be integrated as an open system into any other system. They can be used for any acceleration, vibration or angular velocity measurement application and are designed according to the customer’s requirements.
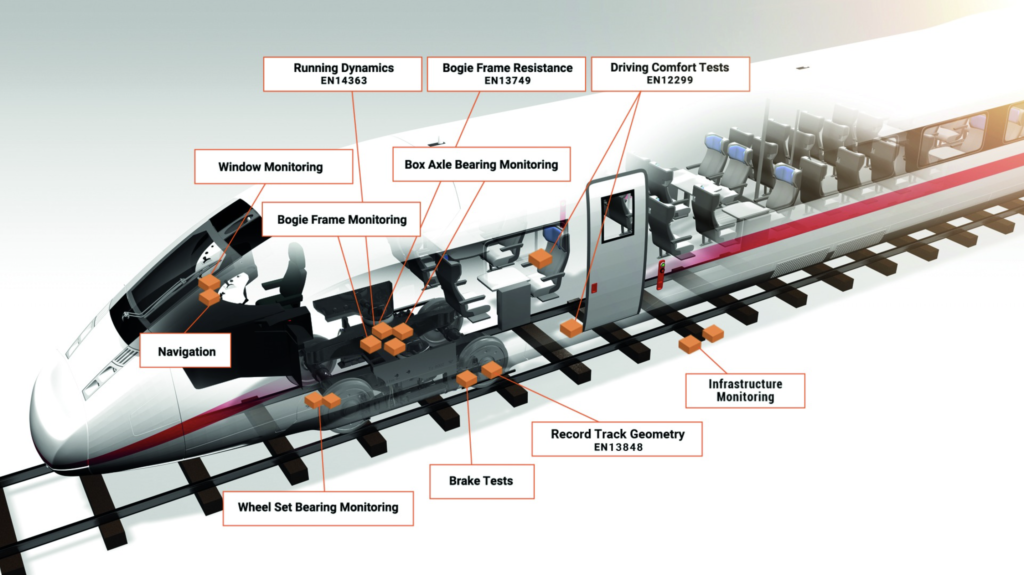
Intelligent Sensors Transmit Data in Real Time
Previously, data used to be recorded externally and evaluated at intervals. With the new smart sensors from ASC, processing is done directly on the sensor, which then issues a status message using the traffic light principle. Rail network operators can now monitor the condition of rolling stock and infrastructure in real time and detect irregularities even more quickly. This keeps the number of service interruptions down to a minimum, as interruption-free operation is the basic prerequisite for more intensive utilisation of railway lines. Deutsche Bahn’s overarching ‘Strong Rail’ strategy is aimed at helping achieve the German government’s transport and climate policy objectives. ASC sensors can therefore indirectly contribute to the shift of traffic from road to rail.