New Approaches to Railroad Bridge Monitoring
Over 25,000 bridges across Germany fall into the accountability of the 13 employees in the bridge monitoring department at DB InfraGO AG. An intense task and extreme responsibility. Supported by ASC Sensors’ expertise, the DB bridge experts are currently working on an innovative pilot to make the monitoring and proactive maintenance of critical railroad bridges simpler, safer and more cost-effective in the long term.
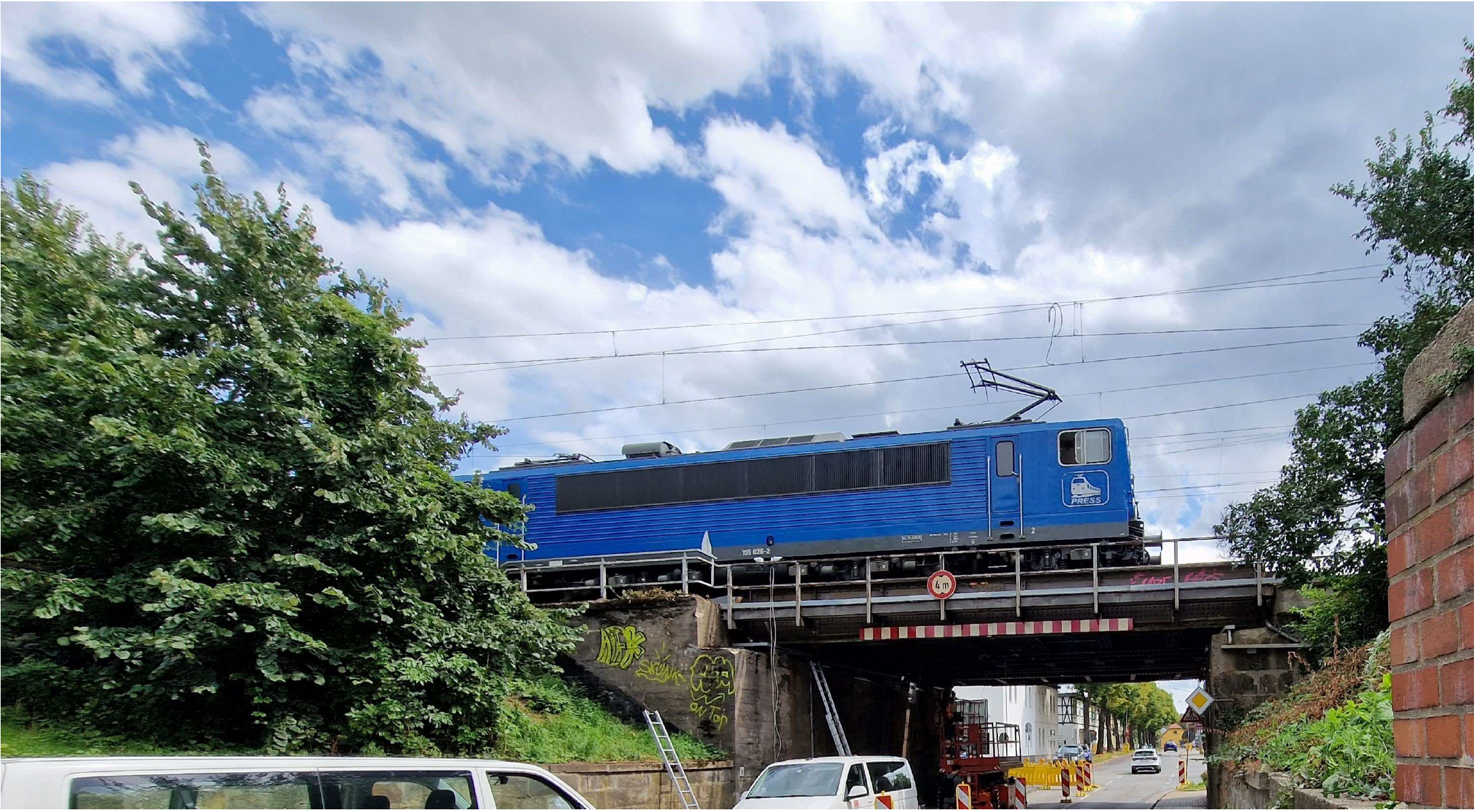
Spontaneous Measuring Usually Interrupts Rail and Road Traffic
Reports Engineer Peter Krempels, Team Leader of the Measurement Unit at DB InfraGO, said:As soon as a system operator or bridge inspector on site notices an unusual change to a structure, or merely suspects one – we are notified.
The measurement team then moves out to the affected structure with the required equipment. In order for conventional laser monitoring to be carried out at relevant measuring points, sometimes difficult terrain has to be overcome, such as heavy vegetation, riverbeds or rocky mountain slopes.
Minimizing or Preventing Operational Interruptions
Bridge measurement is always complex. It requires time, qualified staff, extensive material and often widely laid out cables.
The measuring expert says:Everything we do has an impact on regular operations. In the case of railroad bridges, the entire traffic of the crossing partner underneath usually has to be blocked for taking measurements from below.
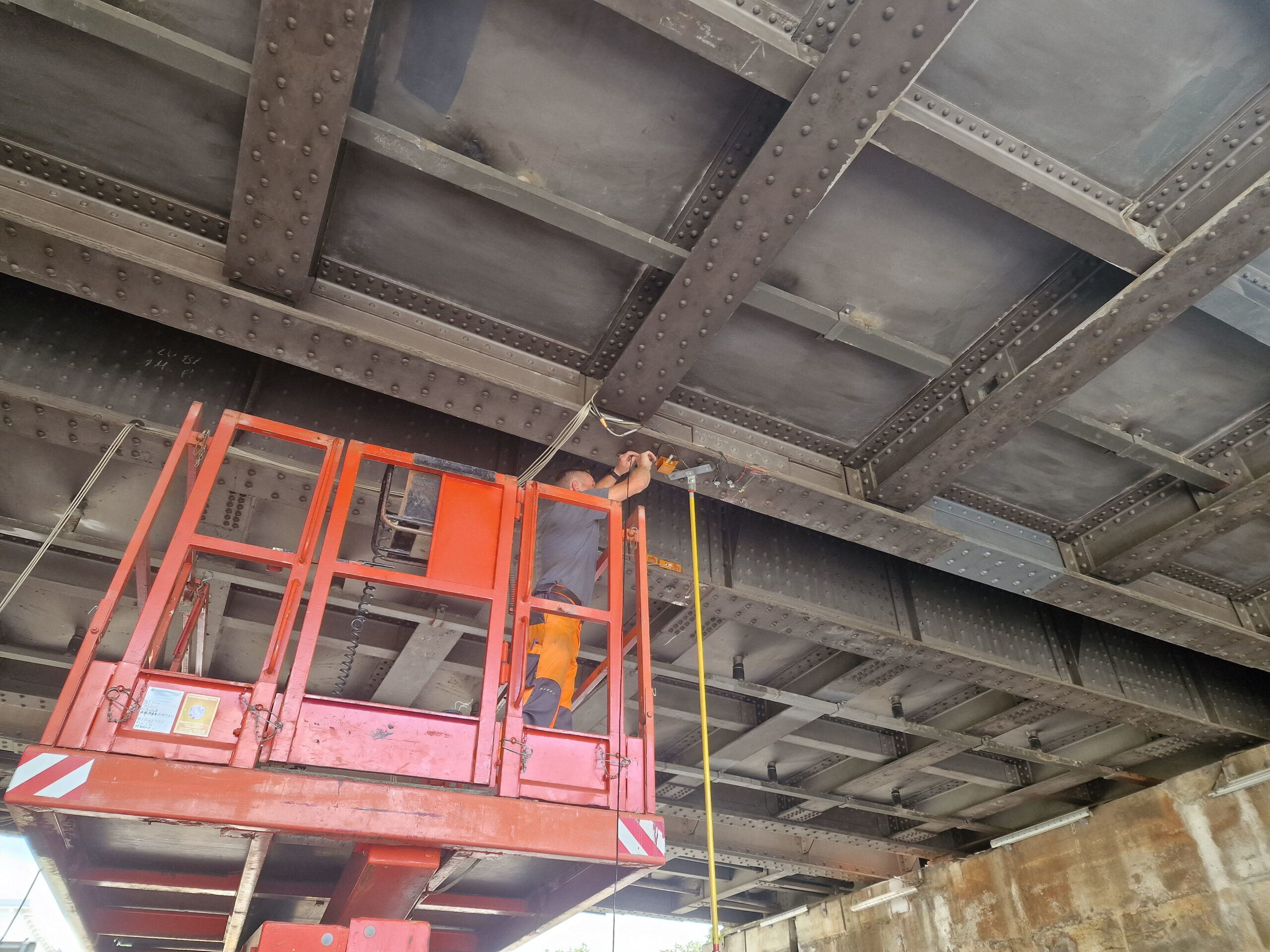
This is the case not only during the actual measurement work: In case of acute risk to the stability and/or operational safety of a structure, the bridge should be closed immediately until the suspicion has been dispelled by a measurement-based recalculation – or suitable repair has been completed.
Krempels explains:Following the examination, the operator receives a detailed report with technical recommendations for the continued safe operation of the bridge.
With older bridges in particular, this can lead to expensive, long-term disruptions of operations. We want to minimize or prevent these through an innovative new measurement concept using smart sensor technology, which we are currently testing in a pilot with ASC.
Smart, Flexible Sensor Technology Enables Continuous Monitoring
To that end, smart sensor systems of the ASC AiSys® ECO series are specially tailored to the diverse conditions of a wide range of bridge structures. Apart from the materials used, the type of construction, its length and many other factors play a role. “No sensor model covers all requirements. The flexible configuration of sensor systems is therefore an advantage.”
ASC Development Engineer Esey Gebreyesus says:ASC's innovative MEMS-based accelerometer system offers a complementary approach to traditional reference-based monitoring methods.
By providing accurate, real-time dynamic displacement measurements, our system enhances the monitoring toolkit without need for fixed reference points. This feature simplifies installation and increases measurement flexibility, making it a valuable addition to the existing methodologies.
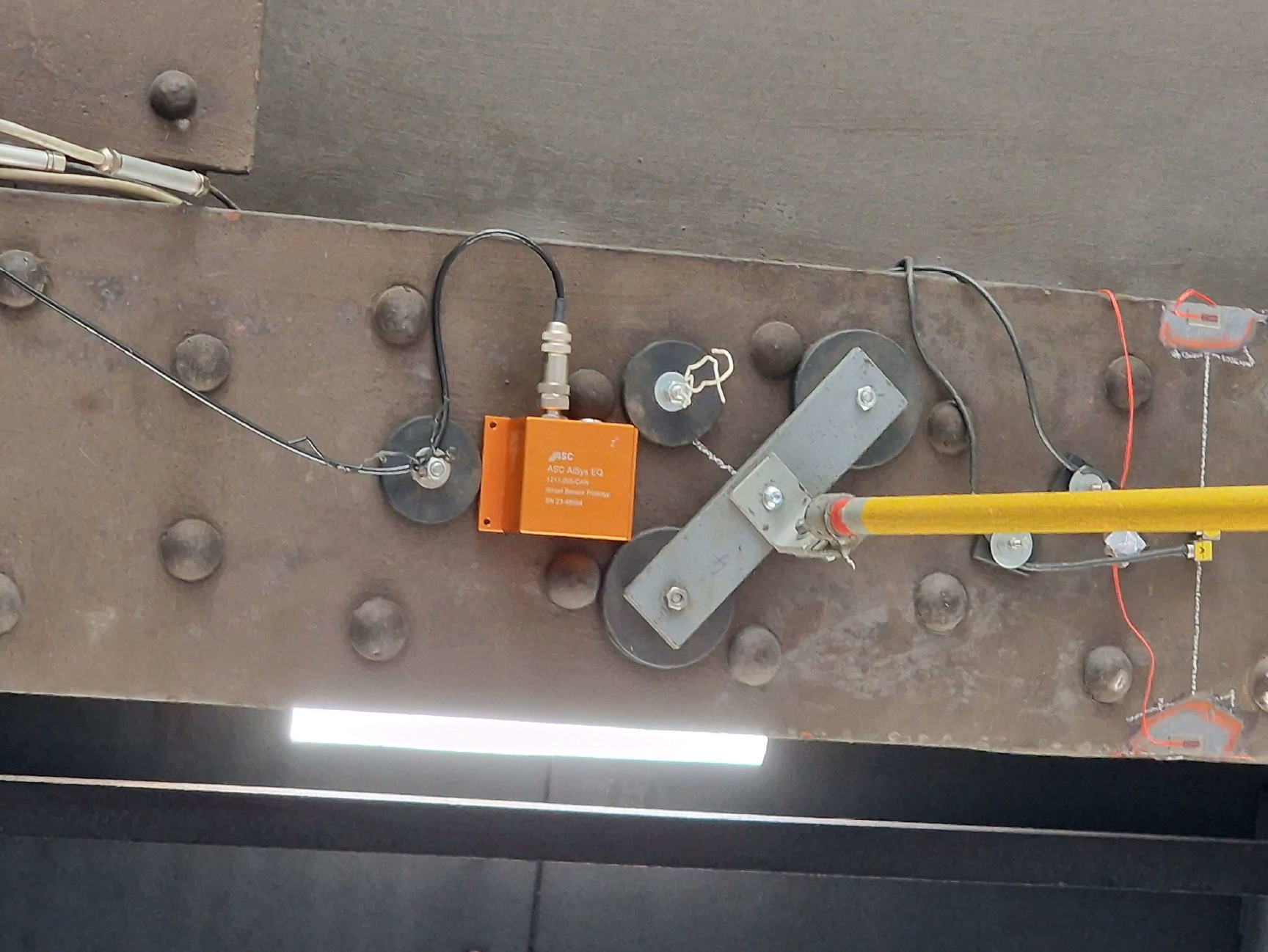
A key indicator of the condition of a railroad bridge is its deflection. This serves as the basis for the structural calculation of the load-bearing capacity.
Krempels says:If, after decades of use, the standard deflection under the same train set at the same speed increases from 1.5 to 1.7 millimeters, then you have to find out why.
It could be a consequence of the outside temperatures or the train load ... but it could also be the onset of material fatigue.
Conventional laser measuring methods offer a direct but very complex method for recording static and dynamic deflection. In addition, it is first necessary to estimate when and where measurements are required. The teams of ASC and DB InfraGO are collaborating on an alternative, to continuously monitor structures in question going forward.
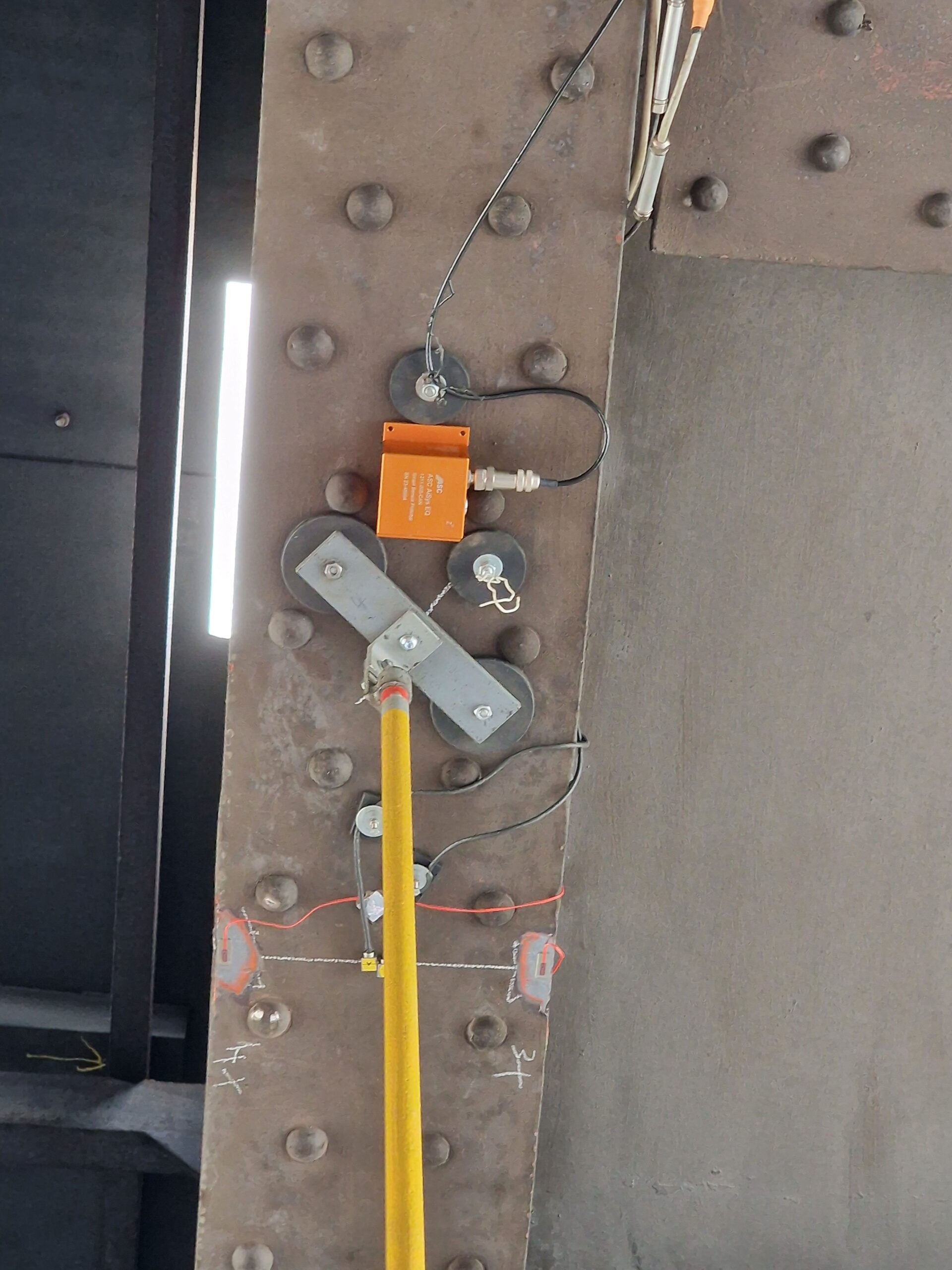
Distinct Sensor Properties and Automated Data Integration
Dynamic displacement monitoring plays a critical role in assessing the health and safety of bridge structures. Unlike static displacement, which measures changes in position under constant loads or conditions, dynamic displacement captures how a bridge reacts to variable forces such as traffic, wind, seismic activity, or temperature changes.
Installed at defined measuring points, the sensor systems are designed to permanently monitor all relevant parameters and continuously analyze them in a multi-stage process.
Gebreyesus says:Due to its properties specially designed for bridge monitoring, ASC's smart sensor technology is particularly suitable for the complex requirements of dynamic displacement monitoring.
These properties include:
- High-frequency data sampling
- Adaptive real-time DC offset removal
- Advanced filtering and decimation
- Double integration and drift correction
- Phase correction and artifacts removal
- Integrated processing and data output
In the future, material expansion and other factors will be calculated algorithmically during train passage, and a complete picture of all changes taking place in the structure will be derived. This enables to detect even the smallest signs of change in the substance of the
structure, and to report them immediately.
Automated data integration of ASC’s smart sensor systems is crucial for this to work.
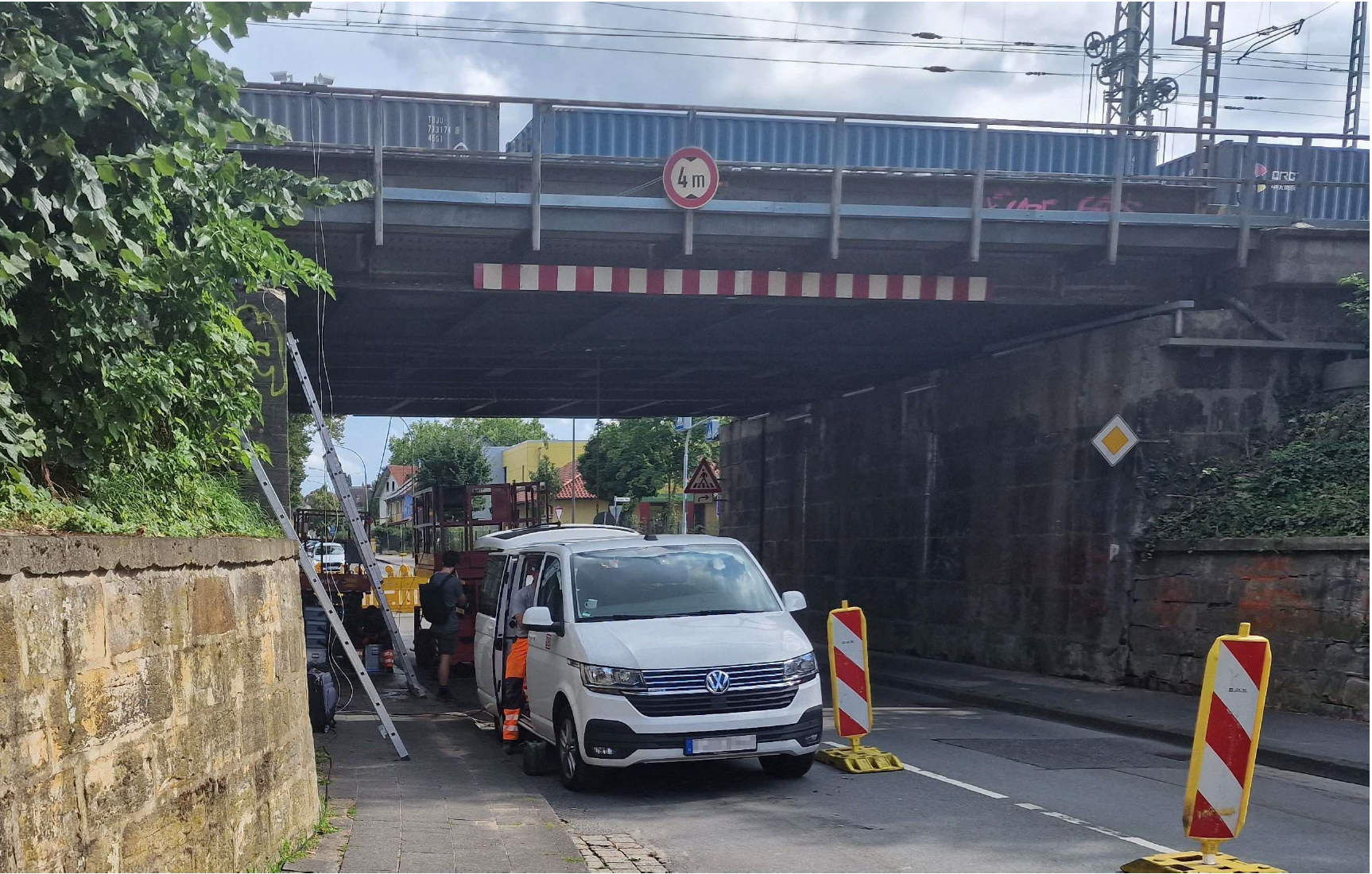
Krempels says:Not only should this enable us to have the results available in real time, but also to receive appropriate alerts and actions instantly.
This is a major advantage for engineers who, with conventional laser methods, would still have to invest a lot of time in analyzing results, meeting to discuss the gained insights and develop recommendations for action.
Early Alert System for Railway Engineers
Krempels says:Instead of waiting for problem reports and reacting individually – at the alert by the local colleague on site who regularly inspects 'his' bridges visually – we want to permanently monitor critical structures and proactively maintain them before acute damage shuts down operations.
“The inability to plan necessary maintenance work is always difficult for infrastructure and rail operators.” Predictive long-term monitoring would therefore be a great asset, especially for bridges that have been in use for some time. “Not only will that approach help identify existing maintenance requirements timely. It will also make them more cost-effective and, therefore, keep many bridges in good condition, operating safely and economically for longer.”
However, it would not make sense to fully equip thousands of bridges of all shapes, materials, sizes and loads with this latest in monitoring technology. This is because new structures are often designed for a service life of 80 to 100 years. “In the first 50 years, you don’t need to measure constantly,” says the experienced engineer. The statistics confirm this. However, older existing bridges may experience unwanted changes or even critical conditions.
Krempels says:We are currently evaluating the benefit of equipping bridges from a service life of around five decades with permanent monitoring
However, ongoing monitoring may be required as part of the approval certification. In particular, this is the case for new, innovative bridge designs outside established standards, where decades of experience and technical guidelines do not yet exist.
Real-Time Monitoring Increases Safety and Service Life
As a condition for reliable, economical long-term monitoring of a building, an exact overall picture of the current condition is first required. This requires a system measurement with a large number of measuring points. Only then can meaningful measuring points be determined that can serve as a reference basis for permanent monitoring in the future.
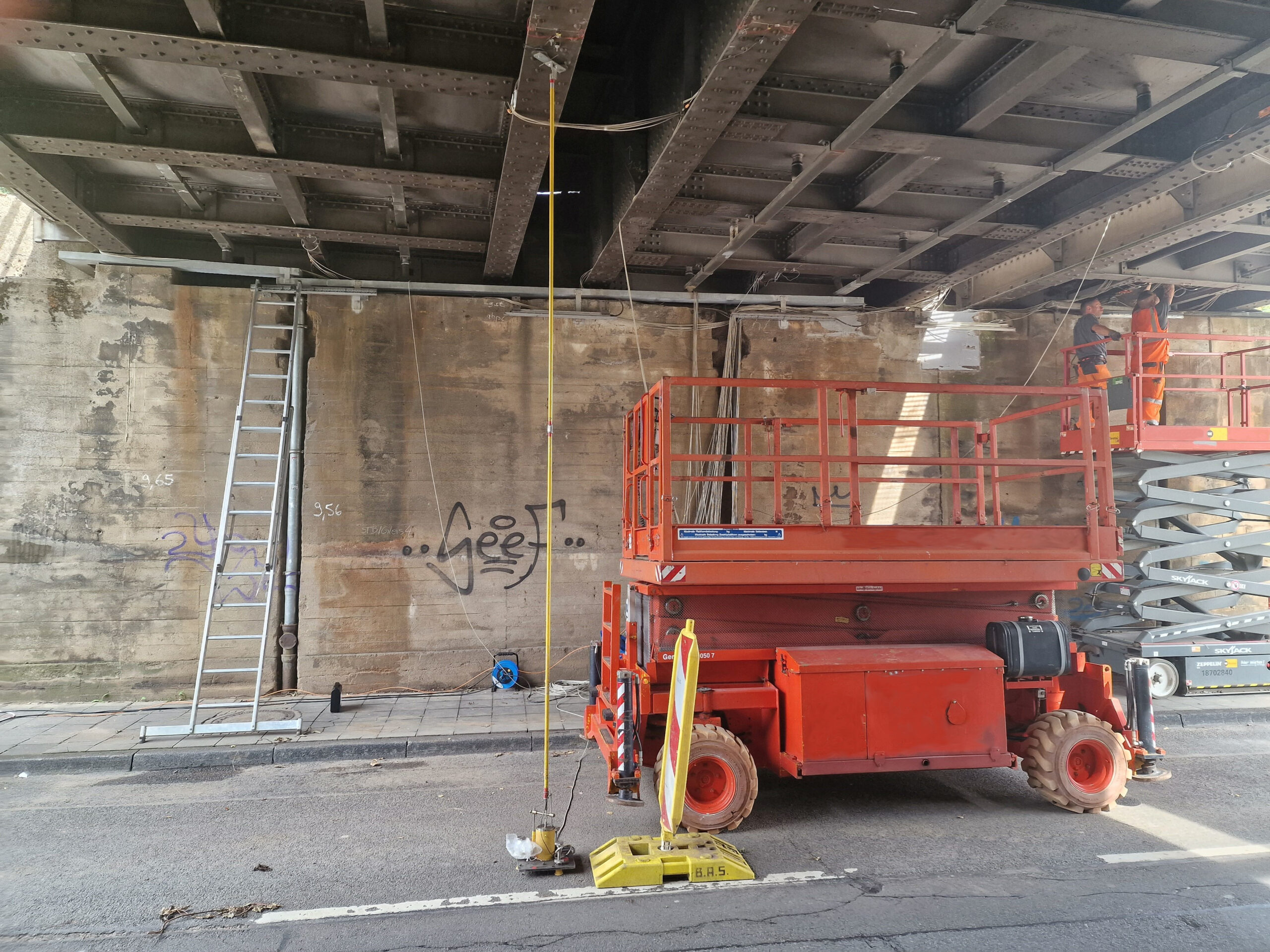
“Conditions are different for each individual bridge. That’s why our test pilot jointly with ASC is critical in order to learn to correctly assess all influencing factors before we go into broader application,” says Krempels. The preparatory work for the constant monitoring of an affected structure can, therefore, take over a year’s time and involves a high initial outlay, but which is soon compensated by significantly lower running costs and, above all, should result in a considerable risk reduction.
One challenge is to keep measurements stable despite a wide range of rapidly changing loads – regardless of train weight, speed, centrifugal forces, climate changes and so on. “This is another reason why we need reliable sensors of maximum precision and long-term stability,” says Krempels.
Flexible Partnership
DB InfraGO’s bridge monitoring team has been in contact with ASC’s sensor specialists for around two years. Monitoring over 25,000 bridges of a wide range of constructions, conditions and stresses is a complex task. “In order to select the ‘right’ bridges for economical long-term monitoring and then switch over from conventional spontaneous measurements, we have been conducting intense tests with ASC AiSys ECO accelerometers for some time,” explains Krempels. “These test series have recently been very successful, so that we can now decide on next steps.”
Krempels recalls:For this innovation in rail bridge monitoring, we were looking for a competent partner who not only had a flexible range of high-quality digital and smart inertial sensor solutions, but was also willing to go down this new path with us.
For example, other suppliers would not be prepared to adapt their standard sensors specifically for our pilot project, adapt software to individual needs or produce small quantities for our test series. “ASC has been able to respond to all our requests so far, has proven to be a flexible partner and invested a lot of time in understanding our requirements and implementing them jointly, despite the small quantities.
This article was originally published by ASC Sensors.