Talgo has developed a new type of running gear frame that reduces the mass of the rolling assembly by 50% compared to those constructed using welded steel plates.
This will be on show at the JEC fair in Paris next month.
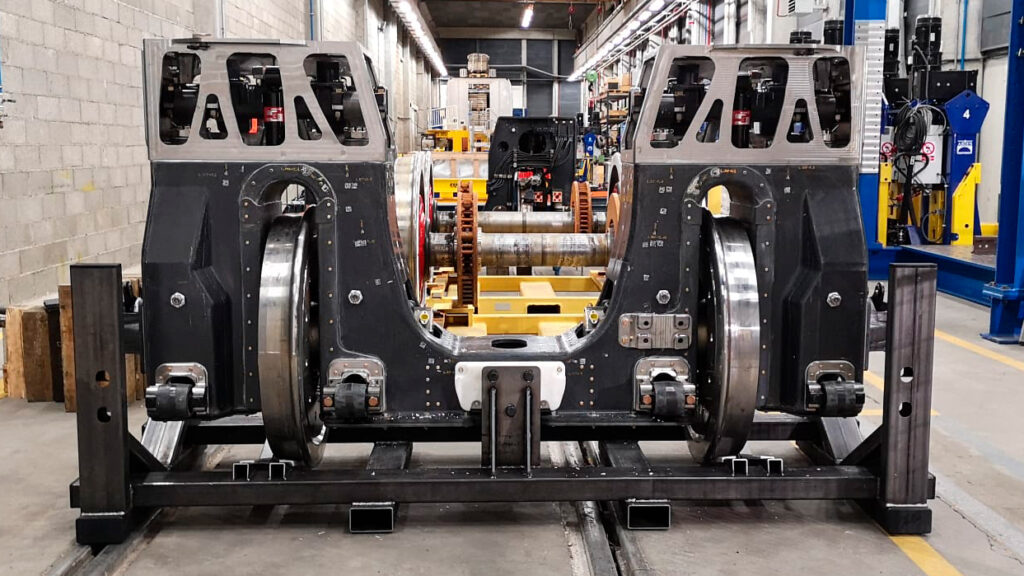
Supported by the European Commission’s Shift2Rail initiative, the running gear frame has been developed for Avril very high-speed trains, but could be adapted for other Talgo intercity or commuter vehicles.
As this is the second-heaviest structural component of the train, and the first in terms of structural resistance requirements, replacing steel with carbon fibre reinforced polymer composites (CFRP) results in large weight reductions with no impact to operating requirements.
Benefits include simplified assembly processes, reduced energy consumption and track wear and tear and an increase in passenger capacity.
Talgo says this concept could also be used in other primary structural components of a train.
Talgo chose CFRP after a careful study of a range of materials and processes. The technology used to manufacture the running gear is based on hand lay-up CFRP prepreg. This makes it fully compliant with the rail industry’s most demanding fire, smoke and toxicity standards.
The rail manufacturer has now completed the full-scale validation of structural requirements according to the current standards (EN 13749). This includes both static and fatigue tests exceeding 10 million cycles, with no significant damage after non-destructive testing (NDT) inspection.
Final acceptance will come once it has been monitored operating under real conditions on track.
The information gained from this work will also go towards helping implement a new set of rail standards around the acceptance process of new materials (CEN/TC 256/SC 2/WG 54).