From materials to coatings, FreiLacke offers everything from a single source
From seat buckets and vehicle accessories to power distribution boxes and rotor blades, the triumphant march of glass-fibre and carbon fibre-reinforced plastics has continued unabated for decades and their applications keep increasing. The main reason for this success are the many advantages of these glass-fibre and carbon-fibre reinforced composites: They are very light, extremely durable, water, heat and cold-resistant and they can be pressed into just about any shape. FreiLacke, the Black Forest-based coating manufacturer, now not only offers diverse coating materials for the surfaces of parts but also the components for their manufacture.
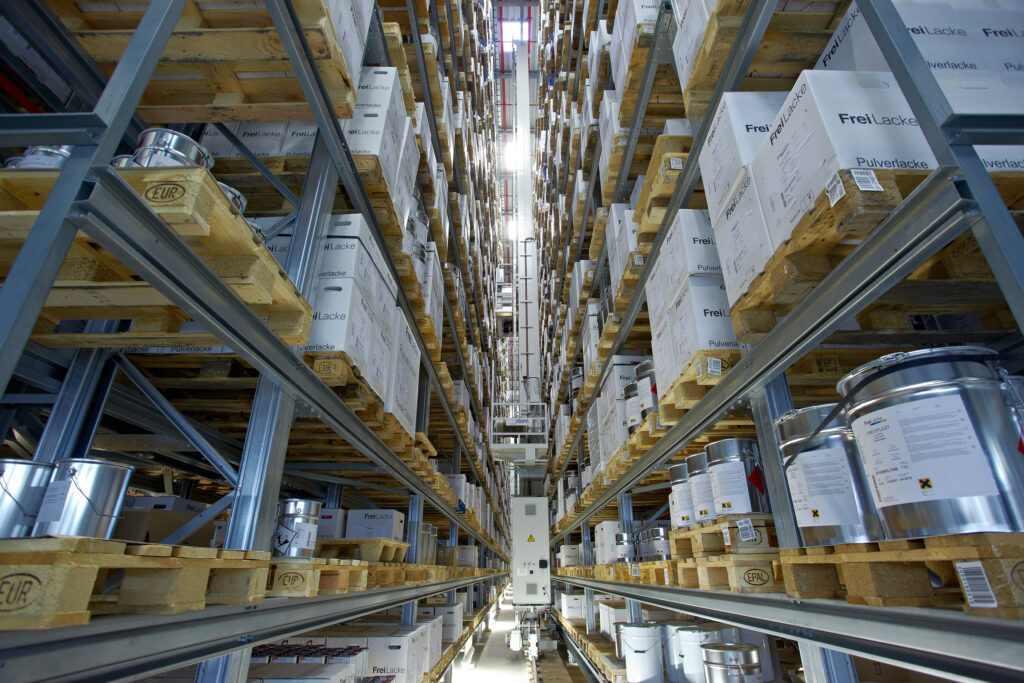
CM Powder for Component Production
One example is the new CM powder technology. Due to a special two-stage principle, this innovative composite powder resin system stands out against conventional resin systems for composite plastics in that it can be melted on without starting the hardening process. That allows them to be processed into so-called PrePregs with complete waterproofing.
Heiko Blattert, FreiLacke’s Head of Development of PG Composites, explains:As a coating manufacturer, we have all raw materials on site and can use them to develop new solutions.
The powder-resin system contains no ingredients that have to be declared and it is free from solvents as well as any harmful carcinogenic substances, which makes storage and transportation much easier. It is available in various colours and reaction speeds and is highly compatible with various fibres, filling materials, inserts and core materials.
Among the applications for the new CM powder resins are the rotor blades of wind turbines. The best part of it: This also allows the blades to be manufactured in a single piece. The previously required bonding process of two individual parts is no longer required, which also eliminates a critical predetermined breaking point.
Coating of Wind Turbines
Rotor blades spin with top speeds of 300 kilometres per hour or more. The aerodynamic profile at its front edges plays an important role because it contributes significantly to the effectiveness of the turbine. These front edges are especially prone to erosion: Environmental influences, such as rain, snow, hail, sand, UV radiation as well as severe temperature and moisture fluctuation, can sharply accelerate this erosion. In the case of offshore turbines, the humidity and salinity they are exposed to can add further strains. A high-performance edge protection coating, which is also referred to as leading edge protection (LEP), is essential.
FreiLacke already has multiple leading edge protection systems available for its customers in the wind energy sector.
Heiko Blattert emphasises:It will only work well if it is matched specifically to the substrate or the coating materials below it.
That is why FreiLacke is offering the complete product range for the coating of rotor blades completely from a single source. In addition, FreiLacke also offers and uses proven coating system structures for the production of the concrete towers of wind turbines. These systems can also be transferred to other industrial concrete coating applications and are already being used successfully in these areas.
InMould Coating with Gel Coats
The company keeps a series of coating solutions for composite materials ready – ranging from colour pastes and fillers to gel coats and top coats. The family-owned business offers them for spreading or spraying on the basis of PU/PUR or unsaturated polyester resins. The gel coats and top coats are coloured coatings that can be applied directly into tools and moulds and provide moulded parts with long-term protection against moisture, UV radiation and impact damage. After it has been manufactured and demoulded, the component is already fully coated. When comparing the PU/PUR coatings to the UP materials, the light fastness and fastness to weathering of the former is much higher.
FreiLacke have also succeeded in significantly reducing the percentage of styrene in the UP gel coats as the substance is deemed hazardous to health and problematic to the environment.
Blattert declares:Using an alternative monomer, we have manufactured a reduced styrene gel coat that delivers even better results than conventional systems in terms of weather resistance and shelf life.
Powder InMould Coating (PIMC)
FreiLacke also offers an exceptional coating expertise when it comes to other composites, such as the sheet moulding compound (SMC), i.e. plate-shaped, dough-like moulding materials made from thermosetting reaction resins and glass fibres. In a single-step production process, electrostatically charged powder coatings that are based on UP resins are applied onto the hot mould. During the hot-pressing process the coating creates a chemical compound with the material. This compound is scratch-resistant, and also extremely resistant against chemicals, graffiti and UV radiation, which is particularly important for outdoor uses. The cycle time is only extended by the duration of the powder coating application and, depending on the component, takes about a minute. After pressing, the finished, coated component can be demoulded. The typical fibre marking is completely levelled out by the PIMC process, the parts are given a highly resistant and very homogeneous surface.
Powder InMould Coating (PIMC) offers a wide range of colours since nearly all RAL colours can be used. That means there is no limit when it comes to the colour range of the components. The material is free from solvents, hazardous substances or carcinogenic raw materials.
Blattert, explains:As an alternative, we developed a liquid coating system that can be injected into the closed mould during the production of the component.
It features very short pressing times as well as high resistances in terms of light fastness and fastness to weathering. The component is ready when using “finished casting” or can simply be coated later on. This also allows applications at the exterior of cars, he emphasises.
Finding Solutions with Our Customers
FreiLacke has long-established itself as a specialist for coating systems and has now gone a step further: With the CM power resins, customers have the option of directly receiving the materials as well as a comprehensive consultation when it comes to the project development and production of the components. And they can count on the expertise of the coating experts from the Black Forest.
Many companies, especially those in the automotive and commercial vehicles sectors, in mechanical engineering, the industrial sector in general and in construction are already counting on FreiLacke composites.
Heiko Blattert believes that a cornerstone of this success is the close cooperation with the customers:Ever since our early days, we have been convinced that true quality of service is only possible if problems and tasks have also been viewed from the customer’s perspective, and are fully understood as a result.
We do not merely support them all the way to series production, but even beyond that across the entire cycle.
This article was originally published by FreiLacke.