Although the Gotthard Base Tunnel represents the cornerstone of the NRLA project (New Railway Link through the Alps), it will be the Ceneri Base Tunnel – for which well-known Italian companies are working – that completes the so-called ‘plain’ railway. Last 27th July AlpTransit Gotthard launched the first phase of the railway infrastructure system lots entrusted to Generale Costruzioni Ferroviarie (GCF).
The Ceneri Base Tunnel
After the opening of the Gotthard Base Tunnel, the 15.4 km Ceneri Base Tunnel represents the second longest tunnel project in Switzerland.
After the breakthrough of the West bore, which took place on March 17th 2015 near the portal of Vezia and which stands out for its extreme precision (only 2 cm difference horizontally and 1 cm vertically), and the subsequent fall of the last diaphragm in the West bore on January 21st 2016, the works are continuing at full speed.
It should be remembered that a large part of the excavation took place simultaneously in both directions from the intermediate heading of Sigirino. To minimise time and costs, the portals of Vigana and Vezia have advanced in the opposite direction, using only construction methods with low environmental impact, since in these sections the works had to be carried out in a sensitive area. The maximum depth of the rock is 900 m, the minimum only a few metres.
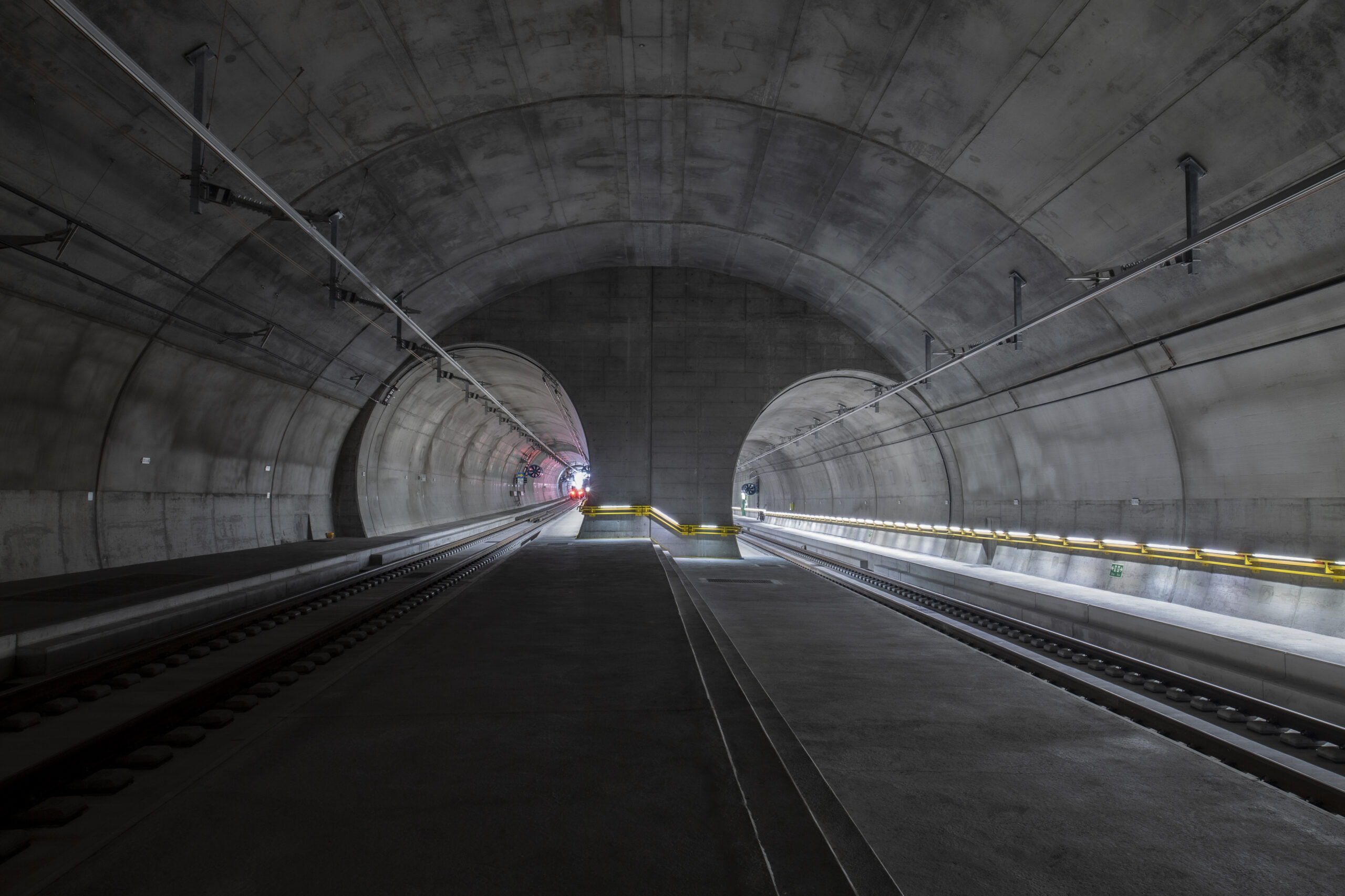
Like the Gotthard Base Tunnel, the Ceneri Base Tunnel also consists of two single-track tubes, spaced about 40 m apart and connected to each other every 325 m via cross passages. Due to its length, no track crossovers or multifunctional stations were needed.
To connect the Ceneri Base Tunnel to the existing railway line, various works are under construction at the Camorino hub. Among them, the four-track bridge above the A2 motorway and the two railway viaducts with the imposing V-pillars stand out. At the request of the Canton of Ticino, the Locarno-Lugano link is also under construction, which will also serve to decongest Ticino regional traffic and reduce the journey time between the two locations from the current 59 minutes to 31 minutes. As for the two main tubes, the tunnel infrastructure systems are being fitted out with mechanical, electrical and ventilation systems, without which the tunnel could not enter into service.
In order to optimise the number of spare parts and certification processes, wherever possible, the same components of the tunnel infrastructure systems used in the Gotthard Base Tunnel were used at the Ceneri Base Tunnel: especially the doors, the ventilation systems and the double floors of the cross passages.The same goes for the special doors of the technical niches (shelters) and, as was done in the Gotthard Tunnel, also at Ceneri the cable-carrying pipes for the high voltage line of the power supply of the traction current of the trains were built directly on the beams.
As regards the runways, the design and construction of the railway infrastructure and construction site logistics was entrusted to ATI (ARGE) Mons Ceneris, composed of Pizzarotti Suisse SA, Marti Tunnelbau AG and GCF SpA.In July, the construction of the railway infrastructure installations began, which called upon concrete mixers from Blend of Rodengo Saiano (BS) commissioned by Generale Construzioni Ferroviarie (GCF) of Rome to be used.
Railway Infrastructure Installations of the Ceneri Base Tunnel
A real “passing of the baton”, after the Condotte-Cossi Group had delivered the Ceneri Tunnel to the client, AlpTransit, in fact, a company 100% owned by Swiss Federal Railways.
After months of design, research and development of innovative solutions, construction site setting up, staff training, acquisition of specialist machinery and equipment, the second half has arrived for GCF, that of putting theory into practice, transforming strategies into action, and projects into actual works.
The Challenges of Ceneri
Almost 30 km of railway infrastructure on concrete, in addition to a dozen kilometres of “traditional” installations on ballast for service links and, also the open sections on the two viaducts and on the link connecting the tunnel to the Lugano-Locarno.The next 12 months of GCF at Ceneri are shaping up to be really intense.
The work process is set to face many complexities: the difficult tunnel logistics on a single track, the extremely limited space conditions, the extreme climatic conditions, with temperatures and humidity rates to be faced constantly and, certainly, the stringent criteria that laying a line destined for High Speed must absolutely respected, since the margins of tolerance are practically zero.
Engineering Solutions for Casting the Tunnel Reinforcement
The test was held on April 28, 2017 in the presence of AlpTransit’s top management and was successfully passed; Blend cement mixers started working inside the tunnel moved by a mobile portal crane developed by GCF. GCF (Generale Costruzioni Ferroviarie) specialises in the sector of railway infrastructures, electrification and signalling; with seven Italian offices and seven foreign branches, it employs over 700 people.
In the base tunnel of Monte Ceneri, where over 150 people will work on the construction site at peak times, on the basis of the project requirements, GCF has adopted a solution that includes the MX08 concrete mixer developed by Blend combined with a mobile portal crane for the positioning of the MX08 at the casting point. A series of advantages that speed up tunnel casting operations. Both engineering solutions (the mobile portal crane and the mixer) have been specifically designed for casting the reinforcement of the Monte Ceneri tunnel.
The GCF Hydraulic Mobile Portal Crane
The self-moving hydraulic mobile portal crane (driven by a Stage IV engine, Euro 6) is able to compensate, by means of a levelling system, the difference in height existing between the two railway platforms. The movement is guaranteed by 16 wheels that ensure correct distribution of the loads (given the huge static and dynamic loads involved when the Blend mixer is fully loaded with 7.5 m3 of concrete) and the movement can be controlled both through a lateral driving position part of the wagon itself and with a radio control; this is achieved with maximum safety thanks to a suitable number of cameras and compliance with all Swiss and international regulations required for tunnel work.
Blend MX08 Mixers
Blend supplied six MX08 agitator-mixers transported by flatbed trains from the concrete production plant to the casting front; the mixers are then taken by three mobile portal crane (each serving two MX08) and brought to the work site at the casting point where, with three swivelling chutes, they cast the concrete to create the slab supporting the track line which includes the prefabricated sleepers.
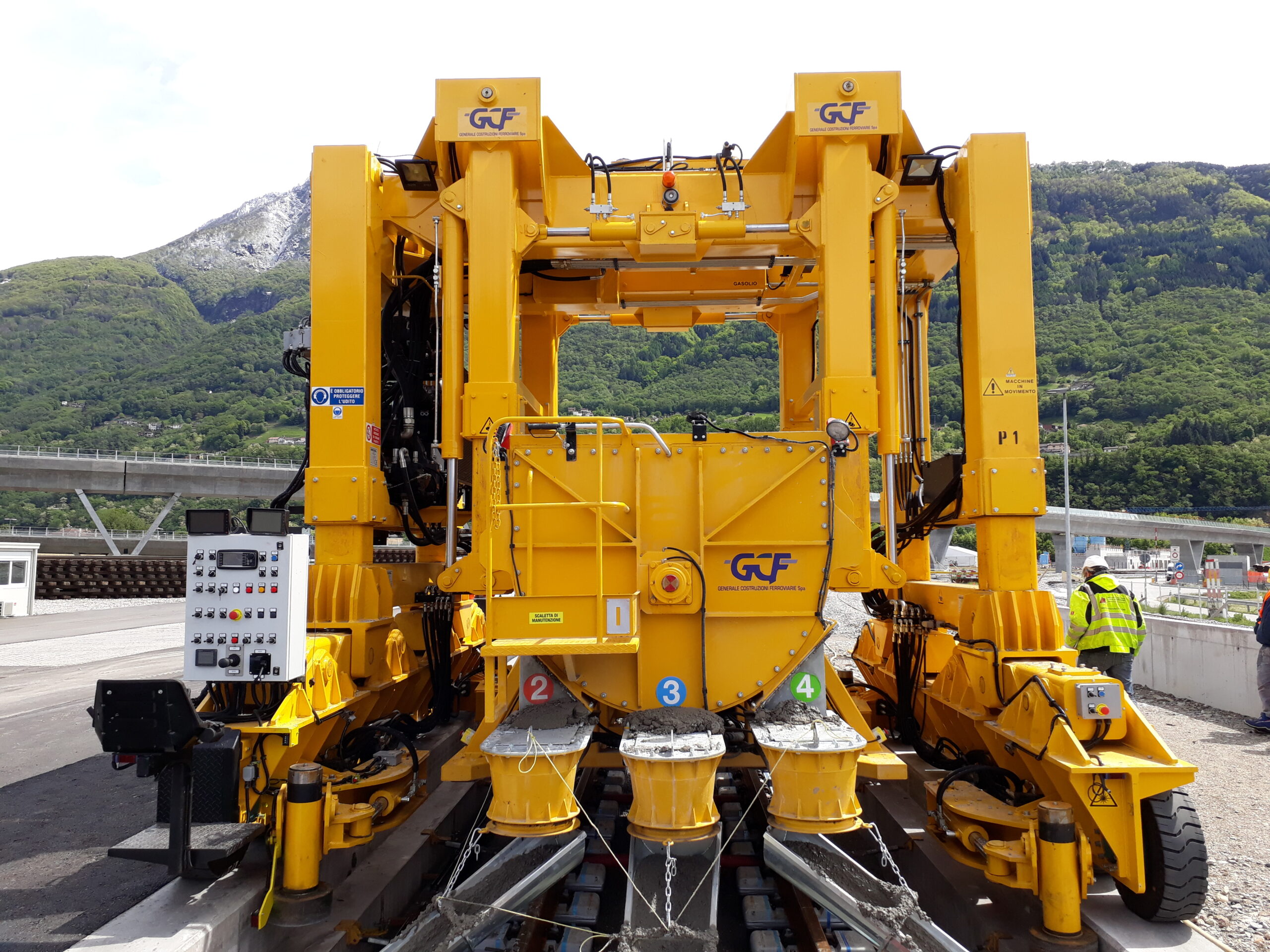
The empty mixer is then returned by the mobile portal crane to the railway wagon up to the concrete production plant. During the return phase, the high-pressure pre-wash system prevents the build up of residual material.
The MX08 mixer was developed specifically by Blend for GCF, on the basis of a detailed range of technological needs, in particular with regard to operational safety and production reliability.
The Technical Features of the Mixer
Blend has developed the MX08 with a dual objective: to maximise wear resistance and simplify maintenance and cleaning operations.
The Company had already built customised systems for concrete casting in the railway sector with the supply for the London Underground.
The Hardox steel tank guarantees a nominal capacity of 8 m3 of concrete mixed continuously by a 1.150 mm diameter auger which guarantees uniformity of the mixing without possible segregation.
The engine compartment and all tanks are located in the rear part of the mixer; the 120 kW motor, with an efficient hydraulic system, always ensures the power required to manage all the functions, i.e. mixing and casting of the concrete.
The casting is managed by swivelling secondary augers which, as mentioned, feed three stainless steel chutes; each auger is combined with a hydraulic piston capable of regulating the flow independently with the shutters according to casting needs. This system does not require the tracks being protected during the casting phase, since the chutes never pass over the tracks.
The MX08 works autonomously in the tunnel: for this reason Blend has installed two large capacity tanks (500 l each) for water, a large tank for diesel fuel and one for hydraulic oil, all well protected against accidental impact.
On the left side of the tank there are three inspection hatches for access to the hydraulic components protected against the aggressive environment in the tunnel.
The hatches allow you to easily adjust the hydraulic flows and therefore the response of the mixer to the commands of the operator in charge of the casting.
Conclusion
Over the last ten months, i.e. since works began on the Camorino construction site, the team of GCF Engineers and Technicians has been adding the finishing touches, not least training Personnel who, during the double shifts planned, will have to work in the tunnel, each focusing on a single highly specialised operation.
Raffaele Forcella, Operations Manager, explained:All the operations have been simulated and tested over the last three months out in the open and then with tests in the tunnel. Men and machines are ready and capable to ensure maximum efficiency.
This has brought the relationship between man and machine and team spirit to an excellent level and will guarantee high-quality work from the very first metre.
Eleonora Gasperini, engineer, said:Once the infrastructure installation of the two bores of the Ceneri Base Tunnel has been completed work on the railway infrastructure system lot will follow in a year that will complete the base tunnel by equipping it with all the necessary systems: contact line, power supply, telecommunications and radio, fire protection and ventilation.
The Ceneri Base Tunnel is scheduled to open in 2020.
This article was originally published by Blend Plants in 2017.