British Steel has won two multi-million-pound contracts to supply 86,000 tonnes of rail to Rete Ferroviaria Italiana (RFI), the manager of Italy’s railway infrastructure.
The agreements – which include the delivery of 18,000 tonnes of its unique premium Stress-Free heat-treated rail – quickly follow two other major deals British Steel has secured with national rail operators.
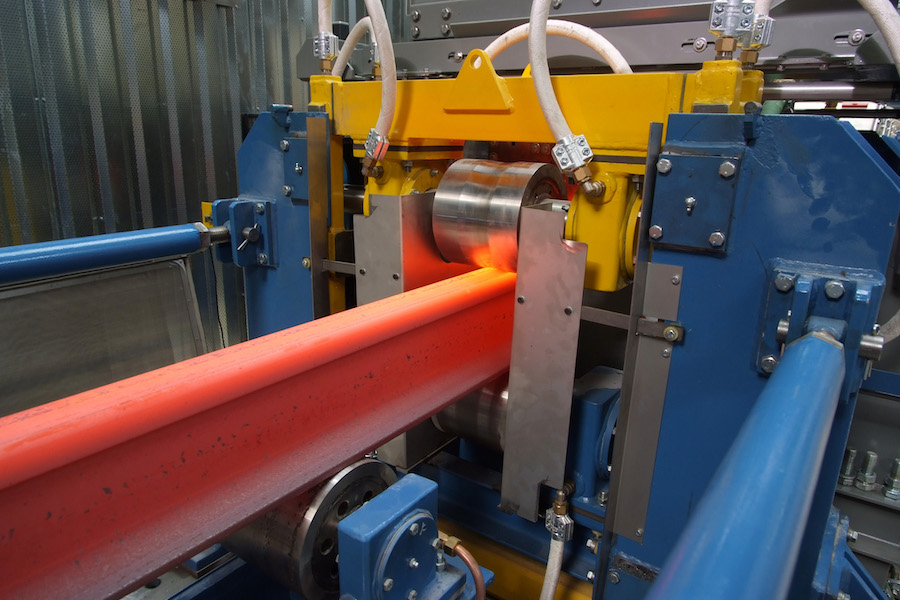
In September, Network Rail announced it was extending its supply contract with the company for two years and in October Infrabel, which operates Belgium’s railways, signed a four-year agreement.
Richard Bell, British Steel’s Commercial Director Rail, said:
“We’re delighted to have been awarded these contracts which reflect the excellent working relationship we have with national rail operators like Rete Ferroviaria Italiana (RFI) and our ongoing commitment to delivering high quality rail in Italy.
“For each of our agreements with RFI, Network Rail and Infrabel, we’ve had to go through a rigorous tendering process so these contracts are excellent demonstrations of our ability to provide first class products and services in highly competitive markets.”
Of British Steel’s latest contracts with RFI, one is for 68,000 tonnes of its standard grade rail and the other for 18,000 tonnes of its premium heat-treated SF350 rails. Both deals are for rail in lengths of 108 metres.
The premium SF heat-treated rails are designed for use in curved or heavy haul tracks where wear and fatigue are significant issues. View a video about our SF rails here.
Richard Bell said:
“Our SF range is increasingly popular as rail is being asked to perform for longer in heavier traffic.
“We developed ‘stress-free’ heat-treated rail to address the industry needs for high resistance to wear, rolling contact fatigue and improved foot fatigue performance to extend the service life of rail and thereby reduce the whole life cost.
“Products like this reduce the need for costly and lengthy maintenance and replacement programmes thereby maximising track availability and allowing trains to run for longer – major benefits for operators and their customers.”
British Steel first made its premium heat-treated rail in 1984 and has since supplied more than one million tonnes of it across six continents – enough to build a railway from London to Beijing.
The steel for the SF heat-treated rails is manufactured at the company’s headquarters in Scunthorpe, England, before being transported to British Steel’s state-of-the art rail rolling facility in Hayange, France. Once there it’s rolled into rails and further strengthened using British Steel’s special heat treatment process.
The unique manufacturing process uses inductive heating followed by compressed air cooling in one continuous movement. This process is so tightly controlled that unlike competitors, no roller-straightening is required afterwards, resulting in a more durable ‘stress-free’ rail.
British Steel’s SF rails deliver a typical threefold increase in the defect size needed to initiate fatigue in the rail foot compared to standard R350HT rails. If fatigue does start, the low residual stress in SF350 doubles the lifetime to failure, compared to standard on-line/in-line heat treatment methods.
Test results showed that to achieve the same fatigue life (5 million cycles) British Steel’s SF rail can withstand 67% more fatigue stress than conventionally heat-treated rails.
Why Choose Stress-Free Heat-Treated Rail?
- Residual stresses in the rail affect how cracks form and grow and controlling this improves the resistance to failure
- The low residual foot stresses achieved during our manufacturing process substantially reduce the risk of rail foot fatigue failure compared to all other heat treatment methods
- European rail standards for R350HT require the foot residual stress to be a maximum of 250MPa – our ‘stress-free’ SF350 rail performs 5 x better than this, with a maximum foot residual stress of just 50MPa
- In typical track conditions, this means a foot defect, such as a corrosion pit, needs to be 3 times larger in SF350 to initiate failure, than in competitor heat-treated rail
- SF350 forms part of our extensive rail product range which includes over 100 profiles, delivering more rail life with less track maintenance
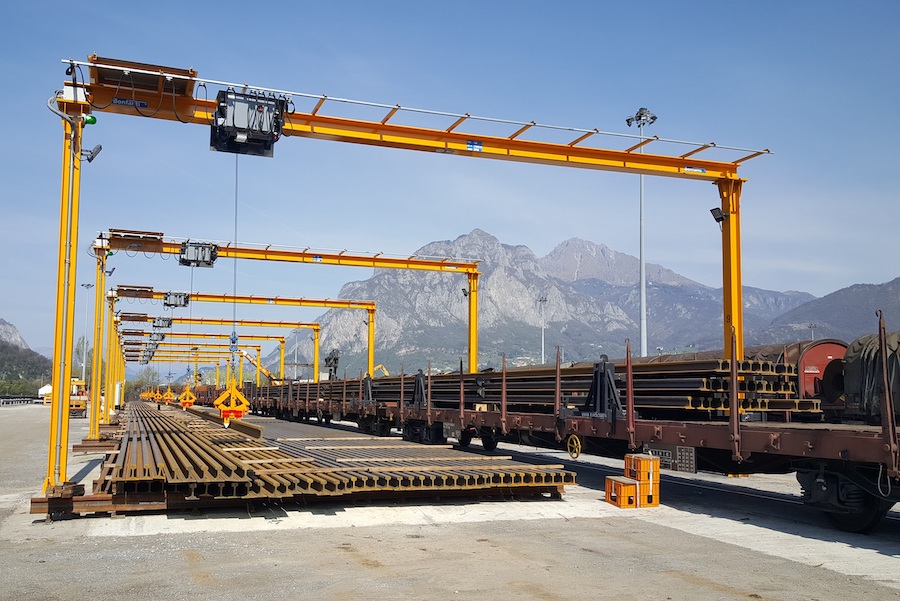
British Steel opened a rail logistics hub in Lecco in northern Italy, last year to service demand in Italy. It can provide a full range of high quality long length rail with just-in-time, and reliable, delivery anywhere in the country.
Richard said:
“Our SF range is another excellent example of British Steel working in partnership with customers to understand the needs of the rail sector and these agreements demonstrate how we can develop innovative and value-adding products to directly address those needs.
“Our technical team is always available to provide advice and support, helping operators to optimise their rail selections. Our rail products and grades can be matched precisely to track conditions, track types, environmental conditions and a host of other variables to ensure that every rail we deliver provides optimum performance throughout its life.”
Richard said: “Our customers recognise we provide excellent quality and reliability and, as demonstrated by these contracts, Lecco is enabling British Steel to better serve Italy’s network providers with premium rail solutions.”