Today’s train operators and manufacturers are challenged by the need for even lighter, more energy-efficient and environmentally friendly trains without compromising safety and durability. Composite sandwich constructions are increasingly used in the railway industry owing to their combination of light weight, high mechanical strength and long service life.
In 2006, Armacell launched a completely new foam core material in the composite industry, a PET-based (polyethylene terephthalate) foam core, called ArmaForm®. After its successful introduction into wind turbine composite applications, ArmaForm is used today in more than 85,000 rotor blades worldwide. And PET foam core is steadily finding a growing market in the railway industry too. With ArmaForm we offer a structural foam core combining high strength with low weight, excellent fatigue and durability, superior temperature stability and excellent compatibility with all common resins and manufacturing methods. Beyond the mechanical properties of sandwich structures used in railway applications, the fire smoke and toxicity (FST) ArmaForm structural PET-based foam core for railway composite sandwich applications performance is a top priority in public transport, even more when trains operate underground or in tunnels. With the introduction of the new European standard EN 45545-2, the requirements for FST performance in core materials have become even more demanding.
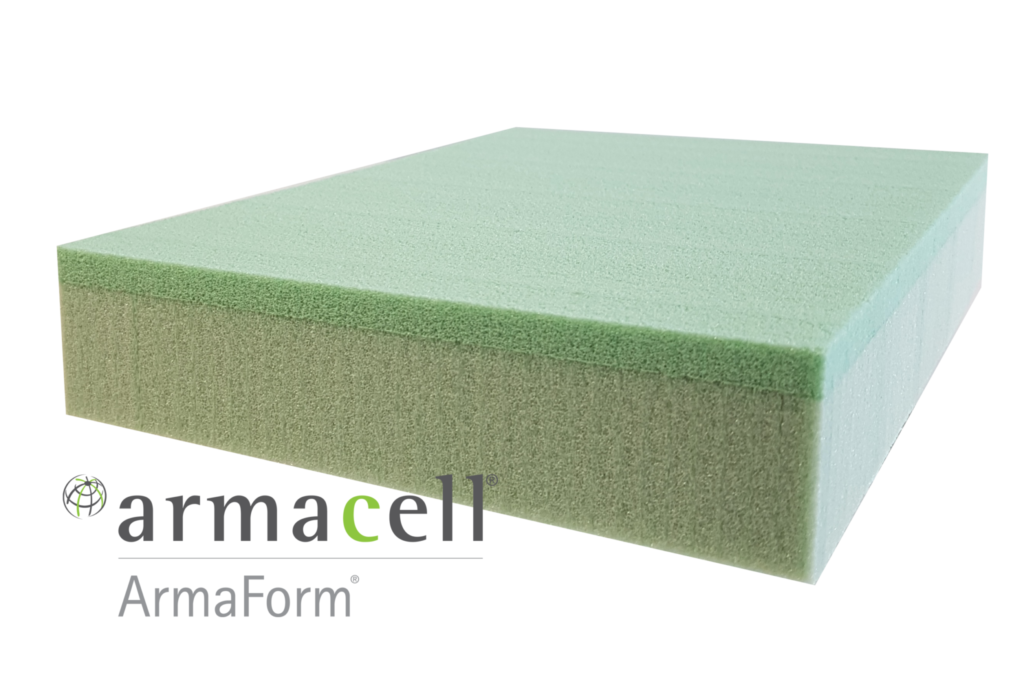
ArmaForm tailored to EN 45545-2 requirements
One of the big advantages of ArmaForm is the very low smoke and toxicity levels achieved when subjected to fire. Armacell offers two grades, the non-self- extinguishing standard grade PET GR and the fire-retarded, self- extinguishable PET GFR grade. Experience in the industry has shown that fire-retarded core material grades are not necessarily needed for trains classified under EN 45545-2. The core material contributes mostly to the smoke and toxicity levels, slightly to heat release, but almost not at all to flame spread, while the skins handle the flame response. Official testing has shown that ArmaForm cored sandwich structures, in combination with appropriate laminates, achieve the highest classification, HL3 – which qualifies the material for use in all types of trains including metro, sleeper and couchette cars. Even in itself (without laminates) ArmaForm pass the EN 45545-2 requirements, e.g. HL2 for R10. Although the standard is not intended to be applied to the core material only, it clearly shows the potential of using ArmaForm in railway applications that need to pass even the most stringent hazard requirements. That would be impossible to duplicate with traditional core materials such as PVC core.
Armacell is offering a ‘multicore’ sandwich solution
ArmaForm MultiCore, part of Armacell’s PET foam core product range, replies to the railway market’s demand for a multiple core design, combining different densities in one foam core to improve impact and point load resistance, while keeping the weight to a minimum. A further key requirement of exterior and interior rail sandwich applications is its impact resistance. Important factors contributing to optimising the impact performance and resilience of the sandwich structure are the core materials’ compression strength, ductility and adhesion to the skins. With ArmaForm all these requirements are perfectly met; comparative testing shows that a PET-cored sandwich structure can outperform traditional concepts like honeycomb as well as balsa- cored structures. The basic property of ArmaForm Core, being thermoplastic, enables novel ways of processing the core. It is known that by using a layered core material with different densities, properties can be improved when it comes to impact and point load resistance for example. However, the extra cost and weight of bonding the core sheets together with an adhesive often offset any advantages gained. With the thermoplastic welding process already in use for PET core, you can economically and safely make “bonding” without the grooves/perforations and adhesive normally required, while achieving a uniformly well controlled bond line every time. Recycling also remains easy as no other material is mixed into the ArmaForm MultiCore material.
In comparing the properties of an ArmaForm with a uniform density of 115 kg/m3, with a multicore solution of densities 200 kg/m3 for the top layer and 70 kg/m3 for the bottom layer, the multicore solution is 13% lighter, while having double the energy absorption for an impact load and a 30% increase in screw retention. This combination of lowered weight and increased impact resistance is ideal for a number of train applications, e.g. floor and nose cone. Different variations of densities will have different advantages, so that ArmaForm MultiCore can be tailored to the different needs of various train composite applications.

ArmaForm – the ‘greenest’ among foam cores for rail sandwich applications
Another high priority for the rail industry is the environmental aspect of trains. Today, designing and manufacturing eco-friendly trains also implies consideration of how the processed materials are manufactured. Armacell is the inventor and owner of the patented process to manufacture PET foam cores made from 100% post-consumer PET materials (recycled beverage bottles), called r-PET technology. A life-cycle analysis has shown that ArmaForm outperforms any other foam cores in terms of environmental benefits. Compared to standard (virgin) PET foam cores, for example, its recycled raw material base reduces CO2 emissions by 33% during the foaming process. ArmaForm enables Armacell and its customers to present a real ‘green’ and cost-effective alternative to other PET and traditional foam cores currently used in railway applications.
ArmaForm is the first fire-retarded PET foam made from 100% recycled PET
Armacell’s patented technology to produce PET foam from 100% post-consumer (recycled) PET materials also started to be applied to the fire-retarded, self- extinguishable grade, called PET GFR. It is superseding the previous PET FR family made from virgin PET resin. ArmaForm GFR grade is now commercially available in a density of 70 kg/m3 with classification M1/F1 according to AFNOR NF F 16-101. The ideal combination of superior FST properties, mechanical properties, cost-effectiveness and environmental sensitivity makes ArmaForm GFR grade the material of choice for railway sandwich applications such as component floor panels, nose cones, interior ceilings and partition walls, doors and much more.