Over the last two decades, maintenance within railway has evolved considerably, influenced by technology, globalisation and the awareness that we have limited resources.
Companies are motivated by both financial and performance-related gain, ultimately increasing their efficiency. They’re always looking for new methodologies and tools – especially considering that maintenance accounts for 50 percent of the cost of ownership. The number of players and the ecosystem has changed considerably: original equipment manufacturers (OEMs) are investing strongly in services, and benefitting from market evolution (in Europe for example). Maintenance services are a natural space for them to move to.
The maintenance ecosystem varies massively customer to customer, but the industry’s shared goal of transporting customers and transporting goods remains. From asset management to maintenance operations, all stakeholders play a key role in the railway transport ecosystem.
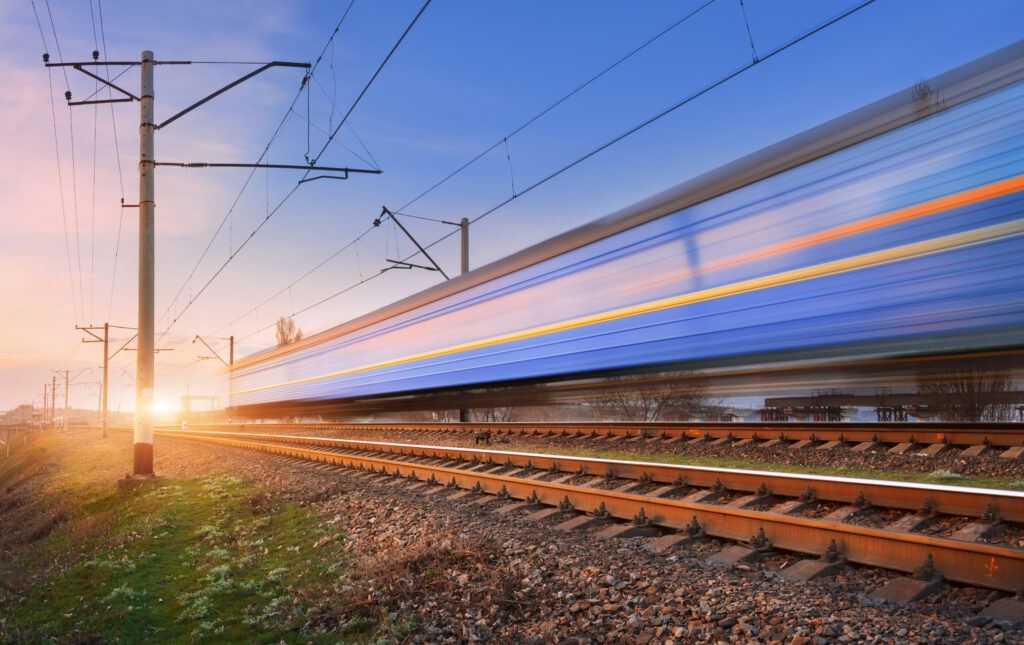
Economic Standpoint
The age of the train operator’s fleet(s) will be an influential factor, considering hardware capabilities and the cost of implementation versus return on investment (ROI). Fleets produced by the main-stream OEMs in recent years, already come equipped with remote condition monitoring devices and have some capabilities (in the worst-case scenario OEMs will do it for commissioning purposes). Slightly older fleets, with digital control systems, train communication network and train control management systems, often come with a relevant variety of sensors for control and have embedded diagnostics capabilities.
However, fleets built before the 90s have very limited (if any) data sources available; making it more costly to retrofit. The installation of sensors and data acquisition modules on top of the on-board devices required for data processing and transmission equate to higher non-recurring costs.
This recent shift with train builders equipping their trains with these systems comes with the pressing need for asset data services in the railway industry. The real drive behind this is that operators were and still are facing some real challenges. The industry is under the spotlight now (for good reasons) with a higher demand, these new tools now inform and ensure that the system’s capacity is at the highest possible level for the required period. Components on the train will always require maintenance and repair, therefore it is about detecting this at the earliest stage with a goal of repairing whilst having the capacity to do so minimising the impact on service.
Train operators considering implementing ROCM should also consider factors impacting the market financially:
- Cloud-based data storage services are becoming cheaper
- Most assets are already equipped with several data sources: diagnostics and operation
- Generalised usage of data services from mobile network operator’s prices are down
- Cost of new sensors is expected to decrease in the future, pushed by market demand
- The Internet of Things (IoT) and the Industry 4.0 era: getting data from your assets is a powerful tool (becoming more common)
- Embedded devices and the edge-computing market are becoming more competitive
Beneficiaries
As stated by McKinsey (Rail) below, OEMs can play a pivotal role within the maintenance rail industry should their services be required. There is an opportunity for them to bid for single tenders and establish themselves within a train operator’s business model, with both parties benefiting from the partnership. However, the three main beneficiaries are:
Urban/Regional Passenger Rail
“Rolling stock OEMs will take on the maintenance for smaller regional and urban rail operators on a service basis, leveraging their currently superior analytical skills and knowledge of the assets and this way putting even more competitive pressure on larger regional and urban rail operators.”
This allows for the smaller rail companies with limited resources (in comparison to large fleets) to obtain expert maintenance from OEMs, assisting asset management and keeping the trains running more frequently, reducing costs and increasing revenue. By keeping their trains running, they can avoid delays and improve their passengers journey experience.
Cargo Rail
“Financial investors increasingly invest in cargo leasing companies who tender the maintenance to the most cost-efficient bidder and offer an entry opportunity to rolling stock OEMs. Next to these players, competition increasingly stems from alternative transportation modes (due to cheap fuel prices and automation in trucking). This situation encourages cargo rail operators to make their maintenance as efficient as possible. The same argument as above holds true for controlling the rail operation’s value chain: large cargo rail operators need to quickly build up their capabilities with respect to condition-based maintenance (leveraging their knowledge of operational contexts) and realise significant efficiencies in their maintenance.”
Freight operators face external pressures and struggle on a market that allows for very small profit margins. There is a cry for efficiency and automation at all levels of the operation. With a ROCM solution in place, asset, operations and maintenance management can work collaboratively together, ensuring train functionality is at the forefront of all operations. With the use of near real-time and historical data, train operators can meet their KPIs by delivering their cargo on time whilst reducing costs.
Long-Distance Passenger Rail
“In long-distance rail, the competitive pressure is significantly lower compared to urban/regional passenger and cargo rail segments. The transportation market is stable, and autonomous passenger cars are still a relatively far-off reality. Customers more and more ask for a higher-quality transport experience, long-distance rail operators might be incentivised to reduce component failures through condition monitoring. This, next to a significant potential to increase margins, might yet make the case, albeit longer-term, for change in long-distance rail.”
Long distance is today seen as a competitive alternative to air travel (for distances <2,000km). It is expected that demand will increase, and governments will promote this move, either by subsidising or cutting taxes on train fares. This encourages the train operator to reinvest in one of their KPIs such as improving passenger experience for example (a common goal within the long-distance passenger rail sector).
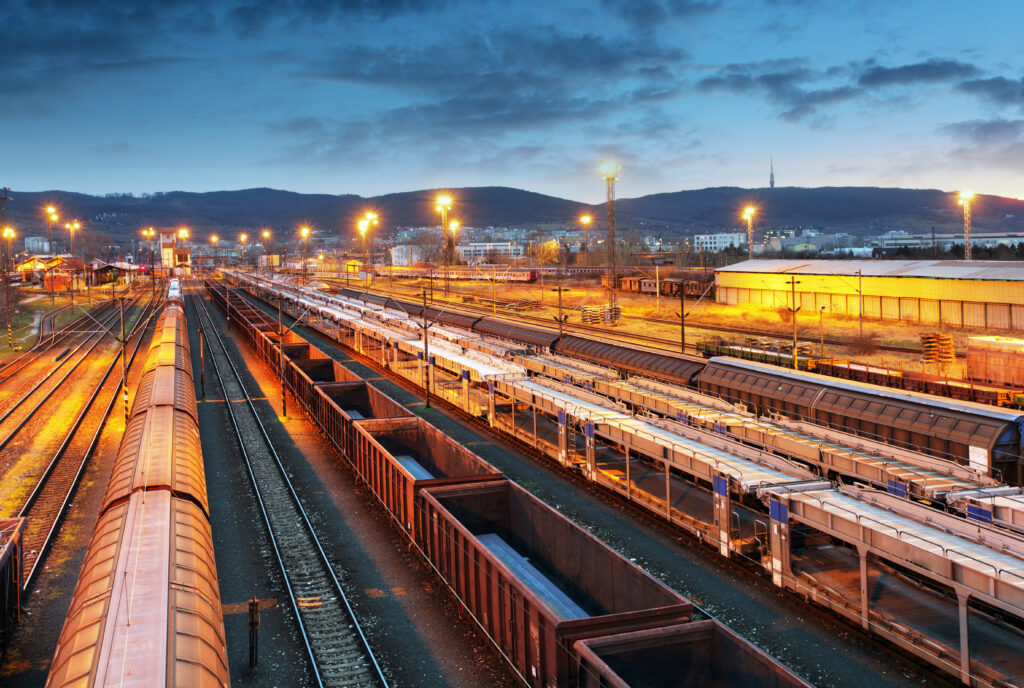
The End-Results
Remote online condition monitoring provides in-depth and real-time information on the performance of crucial equipment and components on-board – partnered with diagnostic alerts – providing fleet operators and owners with the intelligence and sufficient time required to take pro-active action.
Reduced costs and increased revenue are key factors for many but with such a solution implemented, it is about improving the overall reliability of fleets, which is primary. All trains share the same purpose – transportation, but it is how that raw data from a train is used to reap the benefits. With new trains, masses of data can be gathered and organised to then be filtered/enriched, used in artificial intelligence or by experts, impacting business. This data may be real-time or historical – both are important. For example, historical data can be used by reliability management in identifying trends and patterns, whereas near real-time data can be used for alerting operations and maintenance management of any (simple or complex) issues/failures. If the data being extracted is used properly and correctly, the rewards of this are ongoing, with cost savings and an improved passenger experience.
The global rolling stock maintenance market had been assessed at 45–50 billion euros per year and could have up to 5 billion euros per year of potential savings. The maximum additional savings originated by a predictive maintenance programme are not significant enough yet (currently estimated at a maximum of 10 percent). It is estimated that condition-based maintenance can lead to an overall reduction of at least 10 to 15 percent in maintenance costs and increase efficiency.
The financial benefits obtained from ROCM are apparent, the money saved can be further spent on meeting other KPIs and ultimately enabling that both the train service and asset operation are at its best.
With thanks to Nomad Tech, created as a joint venture between Nomad Digital and EMEF, the Portuguese Railways company for rolling stock maintenance.