With Plasser & Theurer’s newly developed rail grinding machine for light rail and trams, rail traffic is easy on the ears: trains travel more quietly on ground rails. The world’s first ATMO (Automatic Track Machine Oscillator) was developed as part of Shift2Rail and combines two working methods.
An Enhanced Rail Grinding Method
When in use, all rails are subject to constant wear. Surface changes such as corrugations and waves occur in different settings: in curves, while braking, and during the acceleration process. In urban environments, such changes cause noise and vibrations. The ATMO combines conventional whetstone grinding with oscillating grinding: the machine employs two grinding saddles, each featuring two grinding stones per rail head. A hydraulic mechanism moves the grinding saddles horizontally, in the longitudinal direction of the rails, with variable frequency. By constantly moving back and forth while travelling slowly, at speeds of up to 8 km/h, precisely fine-tuned grinding is achieved in a single pass. Oscillating grinding is recommended especially for areas prone to developing rail defects. Examples include stations or stops where waves form or other “hotspots” where corrugations occur. The standard-gauge ATMO prototype employs a water- cooled, sound-insulated 100 kW diesel engine with exhaust after-treatment. The engine provides the required oil pressure.
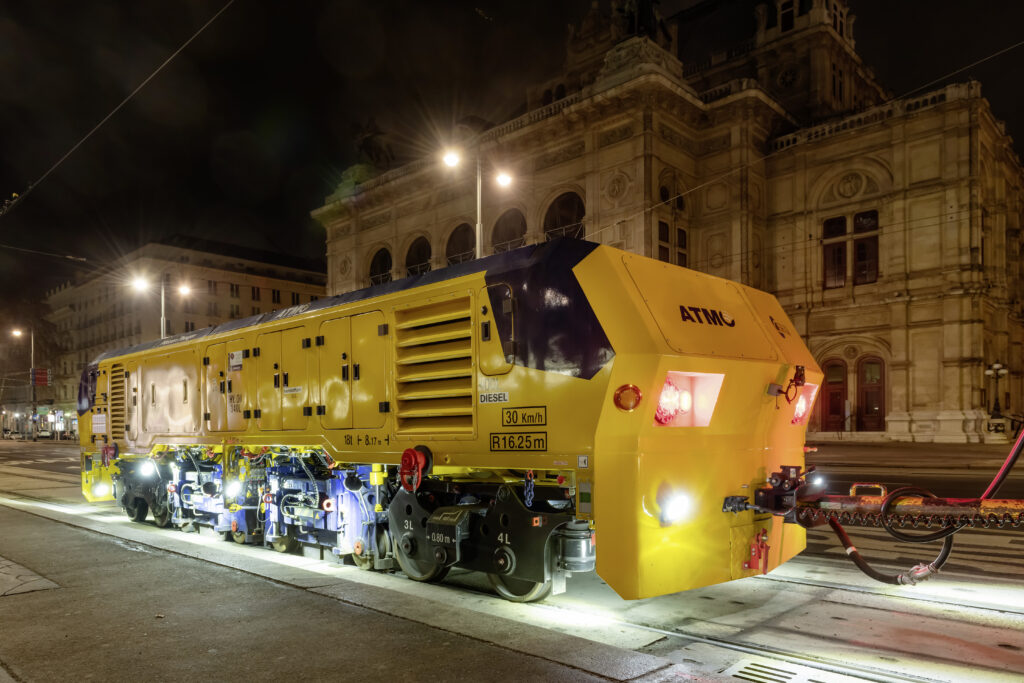
Plasser & Theurer as part of Shift2Rail.
Designed for Urban Environments
The new rail grinding trailer designed for tram networks grinds plain track and turnouts. A power car or road-rail vehicle tows it to the worksite. No staff is required on the rail grinding trailer. It is remotely controlled from the traction unit. In both directions of travel, the ATMO grinds at travelling speeds of up to 30 km/h and blends seamlessly into normal tram traffic. As a result, no line closures are required. Relatively tight curve radii pose a challenge in urban environments. The four-axle rail grinding trailer can work in radii down to 17.25 m and can travel along radii as small as 16.25 m. When travelling along curves, the grinding stones are aligned in relation to the radius in a way that they are always positioned above the rail head. Unlike with conventional grinding vehicles, there is no need to lift the grinding stones when passing over turnouts and crossings. The new machine is equipped with a 2,800 L water tank for wet grinding. The thin water film improves grinding output and prevents flying sparks that pose a fire risk in dry surroundings and tunnels.
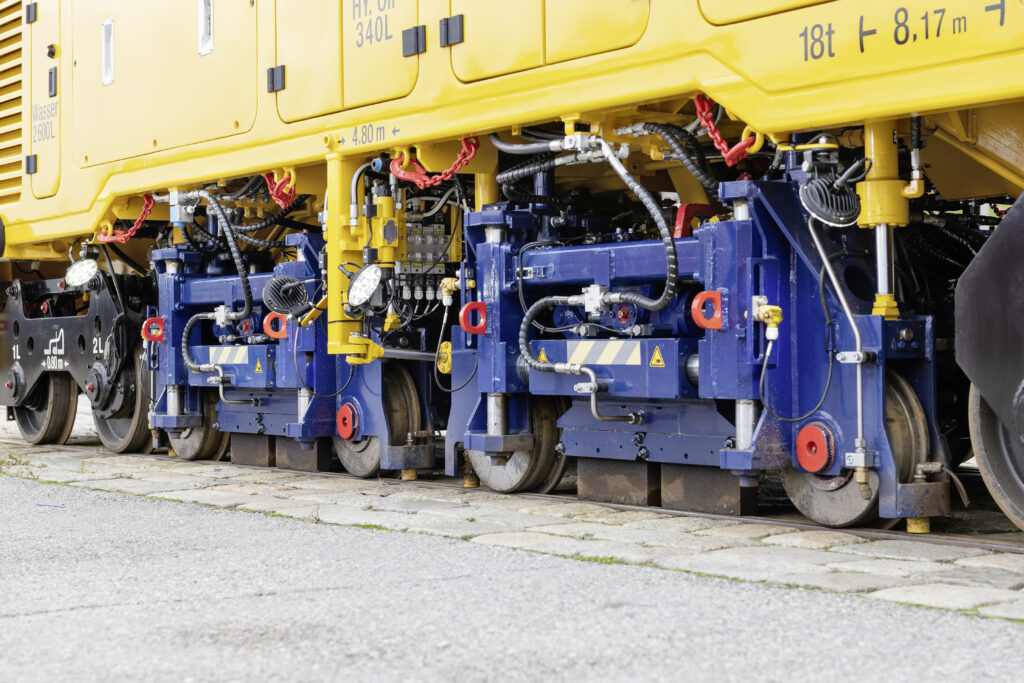
The Research Project and Practical Tests
The ATMO rail grinding trailer was designed with practical requirements in mind. It is the result of a collaboration between industry partners, university experts, and infrastructure operators. A market study conducted by the Vienna University of Technology as part of Shift2Rail forms the product’s theoretical basis. Plasser & Theurer, the industry partner, provided the know-how that shaped its design and manufacture. In mid-2020, the ATMO started its first test phase simulating various conditions on tramway tracks operated by Wiener Linien, the Vienna public transport operator. The European research initiative Shift2Rail (S2R) focuses on any improvement that benefits the wheel/rail system. The Shift2Rail initiative includes the IN2TRACK (I2T) project, which started in 2016. It involves an I2T industry consortium and various partners.