Parker’s Fluidic Solutions team has developed a new product which is transformative in its approach to ancillary systems for rail vehicles.
To fully appreciate the impact of this new approach we first should consider traditional ancillary system design and the issues that can arise as a result.
The typical traditional approach with ancillary system design has been to design a bespoke solution almost project by project. Some efforts have been made to utilise a common system across a vehicle platform, but even then, project variations can lead to system variation and modifications to designs.
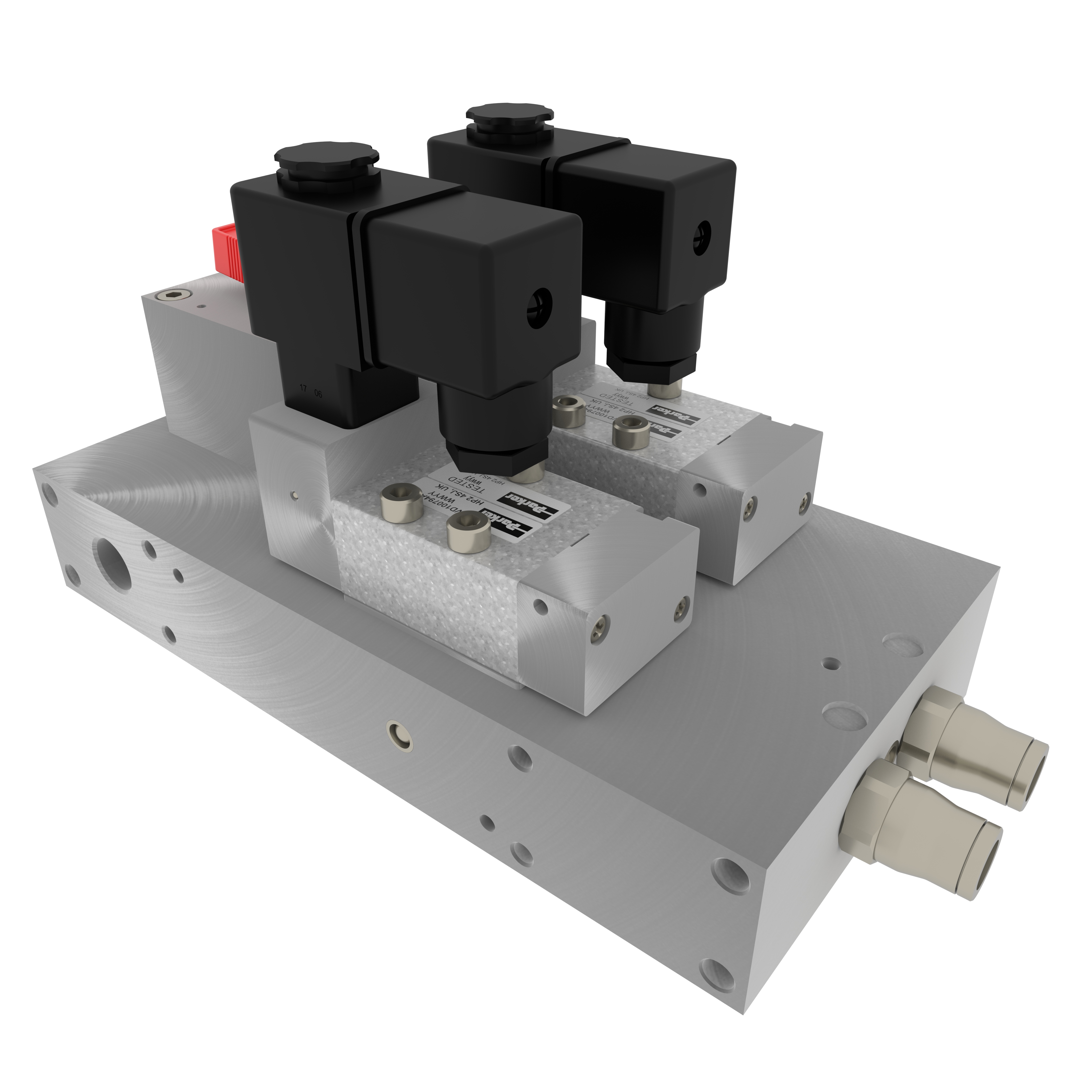
Trying to force the use of a common system without any flexibility to alter its design can be both technically and commercially challenging with the possibility of ‘off system’ additions being required, or conversely component redundancy. This traditional design approach also doesn’t drive a common spares catalogue with the possibility of different components being used on a project by project basis, thereby adding to logistic costs and spares management complexity.
The documentation requirements to support the development of a new system design are significant and include the technical file for the design but also the required manuals, drawings, LCC/RAMS and contractual documentation. With bespoke designs on a project by project basis this documentation can consume significant time and result in one off non-recurring cost charges.
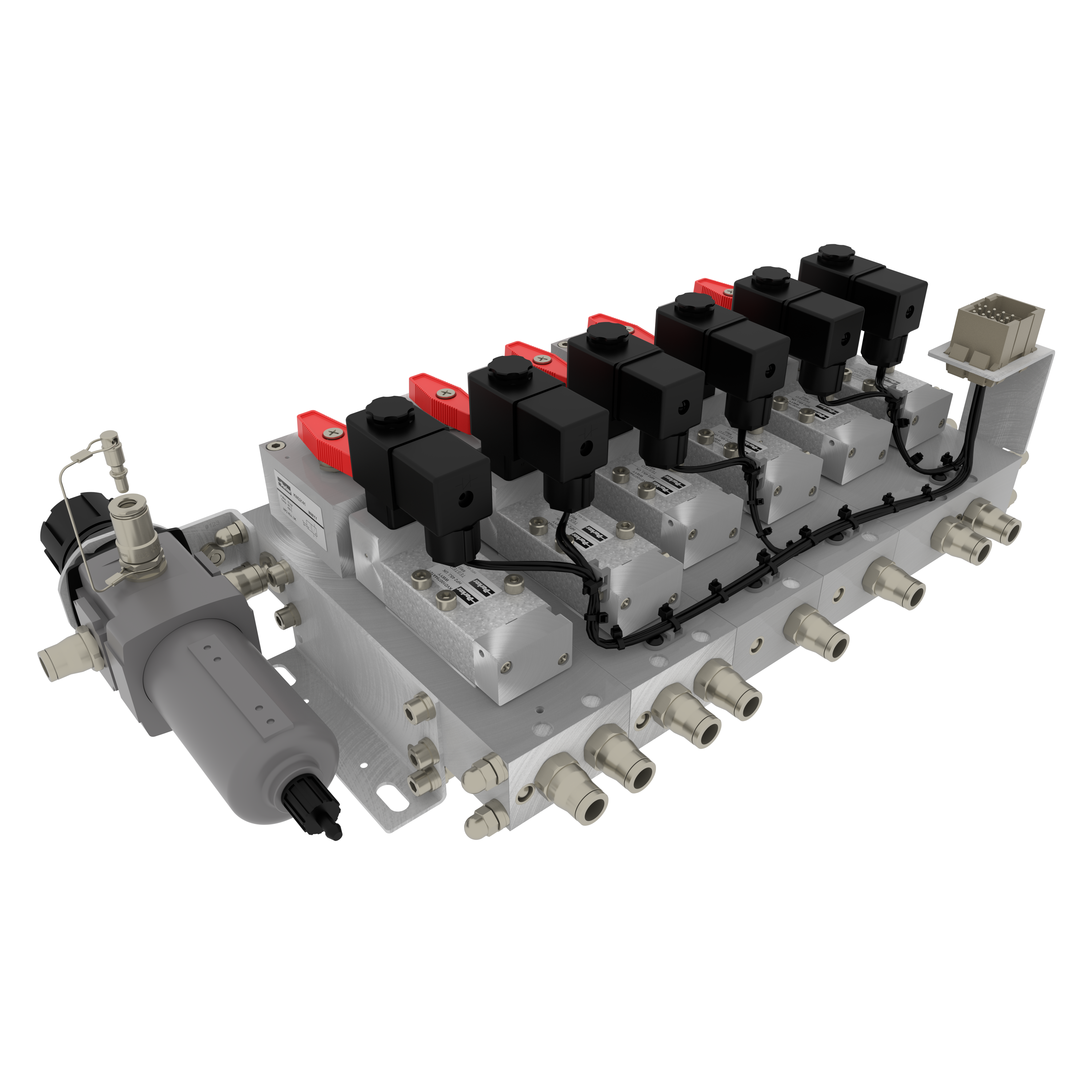
Everything discussed so far has cost implications both in terms of system procurement cost and indirect costs for engineering. However, there are other less visible impacts such as the training requirements for different bespoke systems, the different maintenance requirements and activities and even installation methods and time.
The transformational new approach from Parker has system configuration flexibility absolutely at its core, drawing on a common range of rail industry standard products to ensure standardisation of products and spares across multiple contracts; it looks to address the traditional issues discussed above.
The thought was, take the common functions and make standard sub-modules to address the specific function control requirements. This has led to the design of a range of function blocks that can easily be configured into an ancillary assembly, identify the functions required and configure them in to a fully assembled and tested control system, ready to plug and play.
As well as being able to configure function blocks into a complete system assembly, blocks are designed so that they can be used as stand-alone controls. A prime example is the horn control system, the benefit of which is the ability to then locate the control much closer to the actual application it’s controlling. The blocks could also be split into separate smaller ancillary systems. A benefit of this would be that the control could be placed nearer its application; another is that the available space can be used more effectively so that smaller space envelopes can be considered.
With the new approach, the technical file also becomes standard and is configured to align with the function blocks being utilised, and the same is true for the technical manuals and drawings. For the LCC and RAMS documentation the data is pre-formatted and just needs the project variables such as project life, duty times and current costs to be entered in order to calculate periodicities and costs for maintenance activities. As a result, ‘soft issues’ such as installation and maintenance documentation support are also transformed.
In summary, this new approach means that the time from enquiry to solution is vastly reduced; standard blocks are configured using a standard range of components designed specifically for use in the rail industry. In essence, the benefit lies driving common parts for the spares catalogue and the subsequent benefits to overall logistics management and cost. Utilising a standard range of function blocks also provides for commonality across multiple projects as well as commonality in terms of installation and maintenance activity.
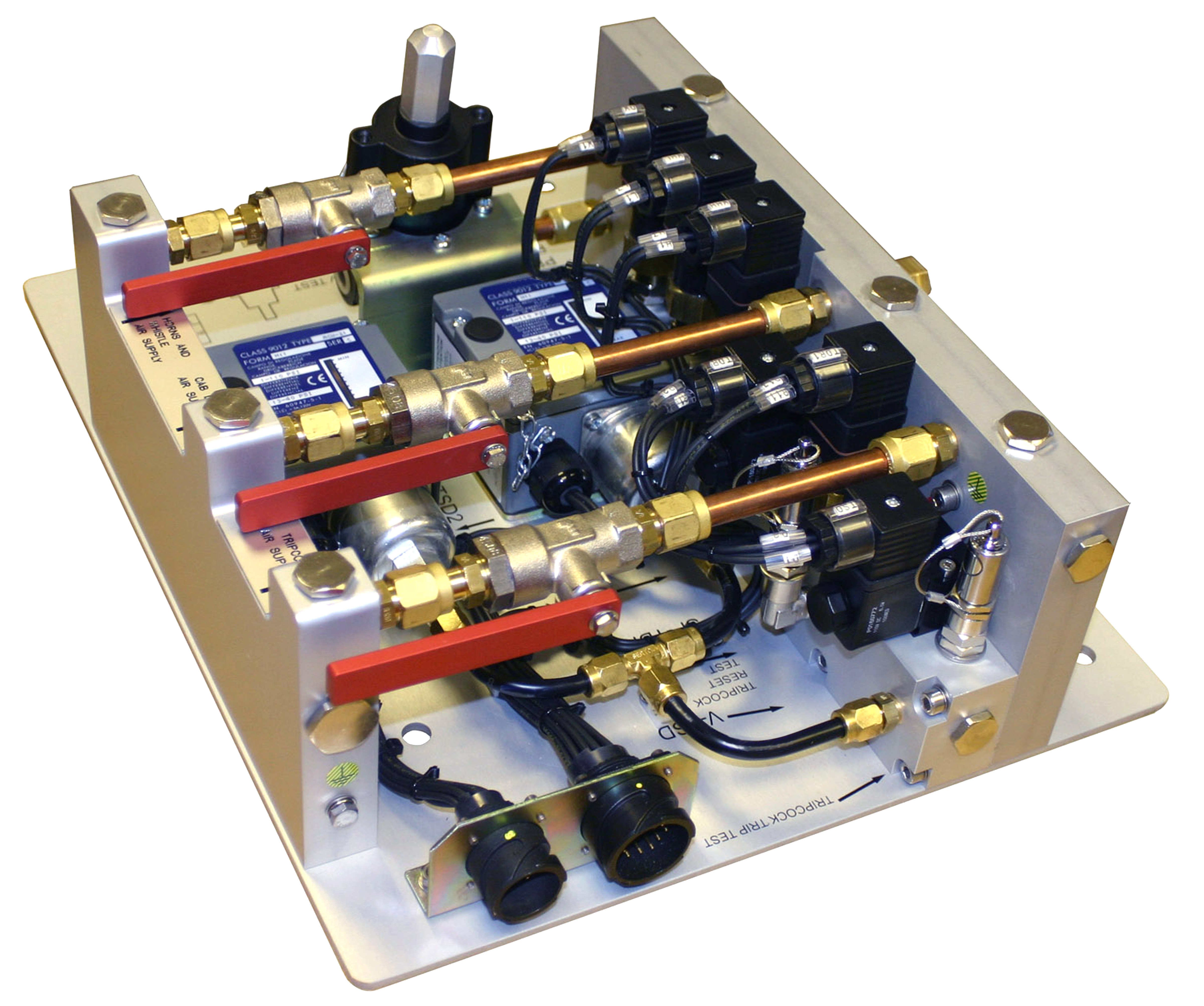
About Parker Hannifin
Parker Hannifin is a Fortune 250 global leader in motion and control technologies. For 100 years the company has engineered the success of its customers in a wide range of diversified industrial and aerospace markets.