Research at the University of Huddersfield could lead to new generations of railway vehicles with carbon fibre frames and key components made using the latest 3D printing technology.
The investigation of novel materials and manufacturing processes is being carried out by the University’s Institute for Railway Research, which has been awarded funding of almost £300,000 as part of an EU-backed project to develop lighter, more reliable, more comfortable and quieter rolling stock.
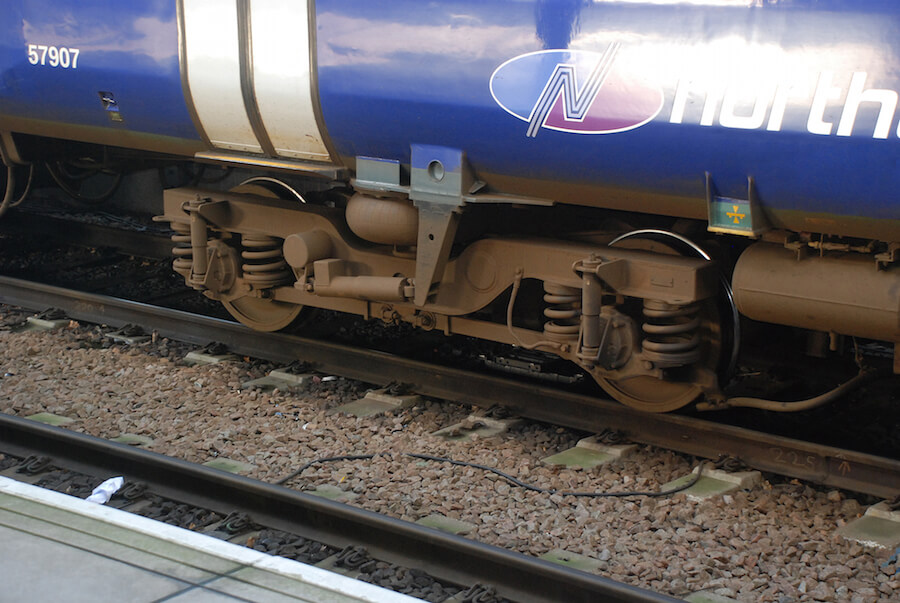
RUN2RAIL Project
RUN2RAIL is the overall title of the new project. It is an element of the EU’s multi-faceted Shift2Rail programme, which fosters research and innovation in European railways. The total funding allotted to RUN2RAIL is €2,732,000, and it has four work packages, shared by leading engineering companies and universities throughout Europe.
The Huddersfield Institute is participating in three of the packages, and is the lead institution for the project to investigate optimised materials for running gear. It will work with the Politecnico di Milano, consultants RINA and the Italian engineering and design company Blue Group.
Carbon Fibre Train Bogies
Professor Iwnicki explained that it was the Institute’s expert knowledge of the design of train bogies and their dynamic behaviour that was being harnessed for the work package. At a kick-off meeting in Milan with the partners, it was decided to investigate the use of carbon fibre composites, which would enable bogie frames to be constructed layer-by-layer by robots.
Professor Iwnicki, said:
You can have any number of curves or shapes and therefore build up the shape you actually want, whereas with a steel frame there are only a certain number of shapes you can make.
Also, carbon fibre is much lighter and you can put the material just where you want it, which makes it lighter still.
3D Printing Technology for Rail
Another strand of investigation will be the use of additive manufacturing – or 3D printing – done with lasers and steel powders. This technology is becoming more mature and components, such as axle boxes and brackets for brakes are now candidates for this process.
Although one engineering firm has produced a train bogie that includes carbon fibre leaf springs, the RUN2RAIL project could lead to unprecedented usage of novel materials in rolling stock construction. For the moment, wheels will probably still be made from conventional steels, however.
Professor Iwnicki, added:
We have considered using alternative materials for wheel hubs or axles, but the failure modes and risks are not yet fully understood. But we are looking at it.
The RUN2RAIL project is now under way and is due to be completed by August 2019.
Original article © University of Huddersfield.
FOR ALL THE LATEST INFORMATION, NEWS, IMAGES, VIDEOS AND ARTICLES ON ALL ASPECTS OF TRAIN COMPONENTS, PLEASE CLICK HERE.