A time-critical track renewal project in tunnels on the Tyne & Wear Metro in northeast England provided a showcase for Pandrol and contractor GPX Engineering to deploy a novel welding technology.
Now 40 years old, the Tyne & Wear Metro network in northeast England is undergoing a significant revamp covering both infrastructure and rolling stock.
The 56 km network which radiates from Newcastle-upon-Tyne was opened in phases in 1980-91. The core of the light metro was adapted from former suburban railways, which were linked together by new construction including a pair of cross-city tunnels, deep-level stations and a bridge over the River Tyne. The subsequent extension to the airport also incorporated a former railway alignment.
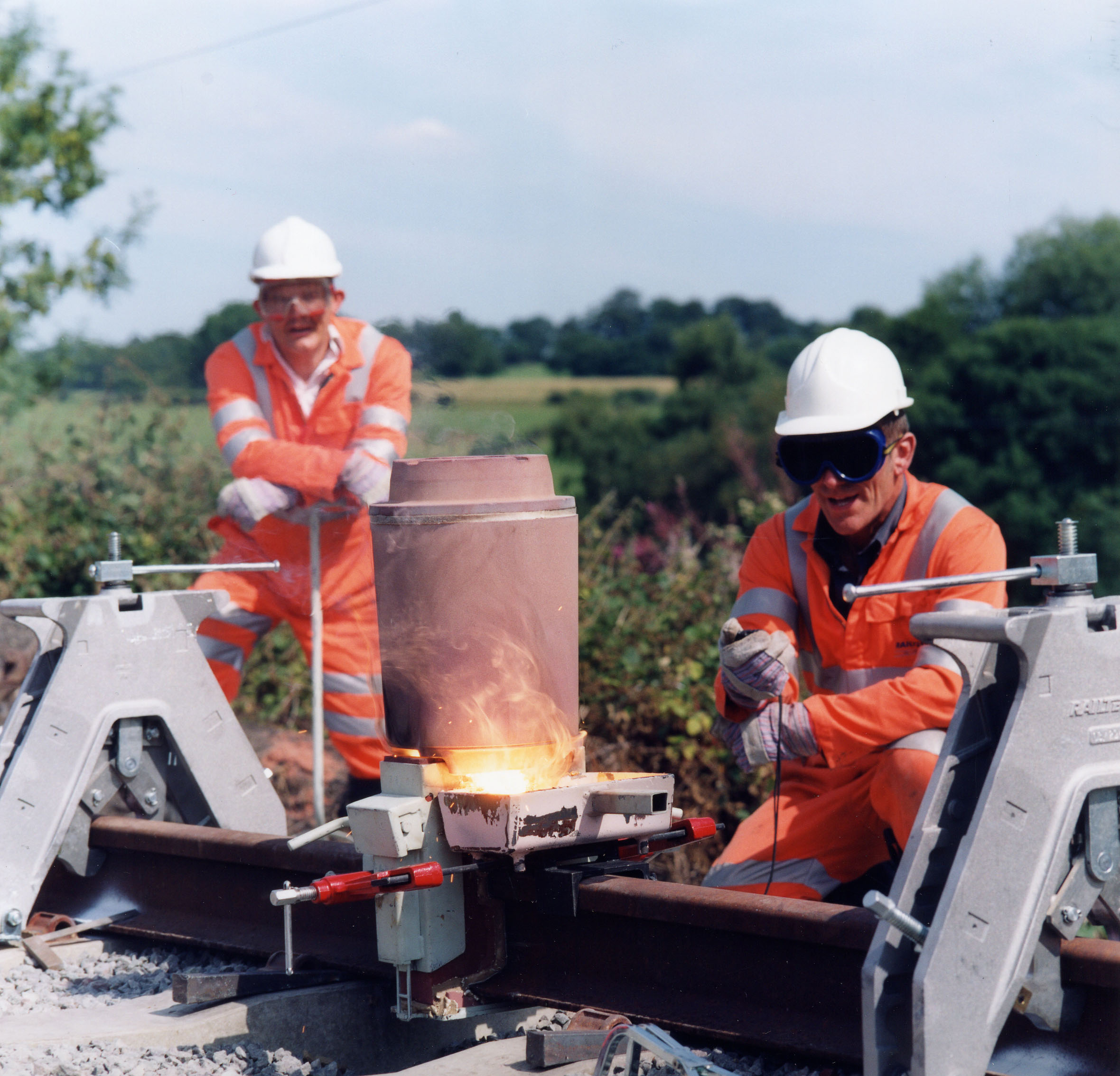
To this was added in 2002 the 18∙5 km South Hylton extension, which took Metro services south to the nearby city of Sunderland. This route is notable as it includes 14 km of mixed running where the LRVs share Network Rail tracks with main line passenger and freight trains.
As part of a programme of infrastructure enhancements being undertaken in phases from December 2019, the local transport authority Nexus undertook extensive track replacement in the tunnels at [Gateshead]. Possession times were short, with access to the track only available between 01.00 and 04.00 on Sunday to Thursday nights. The work needed 140 aluminothermic welds to be completed in a tight timescale.
Contractor GPX Engineering was appointed to deliver the welding services, including inspection and certification. It initially selected Pandrol’s PLA one-shot crucible process, but after the contractors had completed the first few welds on site, Pandrol approached GPX to suggest that that its newly-developed Advanced welding process could help to meet the challenging time restrictions.
Pandrol Advanced brings together a series of innovations at every step of the welding process, offering improved safety, ergonomics and weld quality as well as time savings.
Having looked at the process in detail and carried out a risk assessment that showed a reduced level of exposure, GPX and Nexus agreed that Pandrol Advanced should be adopted for the remainder of the work [mid-February 2020]. A small team of welders working on the project were trained by Pandrol over two days and then supervised on site while they cast their first welds.
Conventional aluminothermic welding involves a process known as luting: sealing the moulds to the rail ends with paste or sand to avoid metal leaks. The Advanced technique replaces this with AutoSeal, which Pandrol believes is the world’s first self-sealing aluminothermic mould. AutoSeal comes with a built-in insulation joint that expands during pre- heating to create a tight seal when fitted onto the rail.
The automated sealing of the mould typically saves at least 5 min per weld. It is also more reliable, especially in cold weather and confined spaces, and the improved moisture evacuation during the preheat phase helps to reduce the defect rate.
Among the environmental benefits, the elimination of luting reduces the amount of plastic waste, and also the material transport requirements. There are health benefits for the staff, as the welder spends less time kneeling and in other stress positions.
The mould rapidly proved popular with the welding team in Newcastle.
Shane Jennings, one of the GPX welding team, explained:It’s quick, simple and saves time kneeling down on the track. The weld is clean and lines are defined, with no blemishes. Collar formation is spot-on every time.
Smaller Crucible
The Pandrol Advanced process uses a small CJ1 one-shot crucible, which is suitable for all standard gap and Head Wash Repair welds, and was deployed for 98% of Pandrol’s rail welds in the UK in 2019.
The CJ1 crucible comes with a pre-installed Startwel electronic ignition system, making it both safer and easier to ignite the charge. By using it as part of the Pandrol Advanced process, Nexus saved on waste and cost; the alternative CJ2 crucible supplied for the original PLA method is 2 kg heavier, and its conventional ignition unit is classified as a form of explosive.
The revised technique also brought a raft of associated efficiency gains. Changes to the internal mould design created a fracture point, so that the welder could simply hit off the vent riser with a hammer after 20 min, instead of having to use an angle grinder. An improved cooling procedure also saved around 10 min per weld, whilst a semi-automatic shearer with ergonomic lifting points was used to remove the excess weld.
The whole process could be managed through the Pandrol Connect app installed on a mobile device, with the welder entering the relevant data before, during and after welding. The details were reviewed by welding controllers and monitored from a central base.
All of the welds on the Nexus project were completed during the allotted night shifts, on time and with no defects. The change of technique saved an estimated 20 min per weld in total, while use of the app improved traceability and cut down on the paperwork.
According to Paul Marshall, Technical Lead at GPX Engineering, the Advanced technology was ‘quicker and more efficient than traditional methods and the failure rate was zero’.
This article was originally published by Pandrol. You can view the project case study on Pandrol’s website.