Making Maintenance Planning More Efficient
Historically railroads have taken a reactive or preventative approach to track maintenance with work undertaken on a fixed schedule or following failure. New inspection technologies provide the opportunity to move to condition-based and ultimately predictive approaches, which offer the potential to reduce costs and maximize maintenance efficiency – the so called LEAN approach.
Between 2015 & 2016 the Canadian National (CN) commissioned Zetica Rail & Balfour Beatty Rail to undertake integrated track inspection surveys of over 590 miles of track on three sub-divisions (Figure 1).
The primary aim of these surveys was to provide data for use in planning the company’s capital maintenance activities (undercutting, shoulder cleaning) and to create a database of potential sub-surface defects (such as ballast pockets) which could be referenced as and when a track defect was reported.
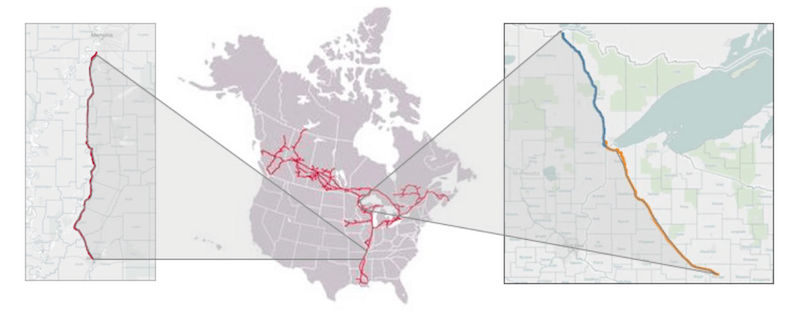
The surveys were undertaken using a Railway Asset Scanning Car system, or RASC®, mounted on a Ford F250 hy-rail vehicle (Figure 2). The RASC® concept involves integrated data capture of a suite of complementary track inspection technologies that together allow a comprehensive assessment of both the above and below ground condition of the trackbed.
Three key systems were deployed: high and low frequency ground penetrating radar (GPR) to inspect the trackbed condition and map the sub-surface layers, a linescan camera system to capture images of the surface of the ballast and a high-speed 2D profiling laser to capture images of the trackbed, trackside assets and the surrounding terrain. The surveys were carried out at speeds of up to 20mph, although the technologies themselves are fully capable of data capture at speeds in excess of 100mph when deployed from a suitable platform (inspection train, in- service train).
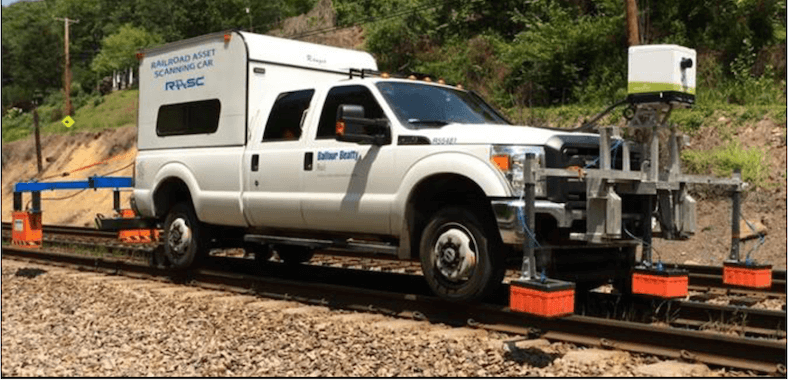
The acquired datasets were located using a combination of on- board Inertial Navigation System (INS) and differential GPS. As well as augmenting the GPS information the INS provided the necessary attitude data (roll, pitch and yaw) required to fully process the laser data.
Processing of the data streams was carried out using Zetica Rail’s bespoke data processing software with the outputs from the three inspection systems reported as a series of trackbed condition metrics, designed to provide an easy means of quantifying the dense and often complex datasets.
The list of metrics generated for the CN survey is detailed in Figure 3. The majority of the metrics are reported over a standardised minimum granularity (typically 5m or 15ft) in order to enable the combination of individual metrics for planning purposes.
In addition to the metrics the surveys also generated detailed geo-referenced 3D point clouds (Figure 4) that could be used for asset mapping and clearance analysis.
Maintenance Planning
Identification of areas of trackbed requiring specific maintenance activities was carried out using a combination of maintenance planning tools including the Combined Trackbed Quality Index (CTQI) and Work Order Recommendations (WORs). The CTQI aims to classify the condition of the trackbed based on a weighted average of selected trackbed condition metrics. This approach is similar to the concept of a Surface Quality Index (SQI) used in the analysis of track geometry data.
The WOR approach goes a step further in assessing the most appropriate type of maintenance activity for any particular section of track using a rules-based approach. The rules are specific to each particular maintenance type and can be customised as required based on the client’s requirements (Figure 5).
WORs were generated for three maintenance types: undercutting, track lifting and shoulder cleaning. The results for one of the sub-divisions are summarised in Figure 6. For each sub-division data clustering was applied to the 15ft results in order to identify minimum-length work packages. Clusters were terminated at the location of fixed assets, such as bridge decks, over which maintenance could not be undertaken.
Geotechnical Information
The integrated RASC® datasets also provide information to inform follow-up geotechnical investigations and plan remedial works. Information on suspected trackbed defects such as ballast pockets and incipient mud spots was collated to provide the CN with a database of locations for follow-up investigation.
Where a more comprehensive analysis of suspected problem locations is required, Zetica provides detailed trackbed inspection reports (TBIRs). TBIRs integrate the outputs from the RASC® survey with other track inspection results such as track geometry, with the objective of highlighting the nature and extent of any trackbed defects.
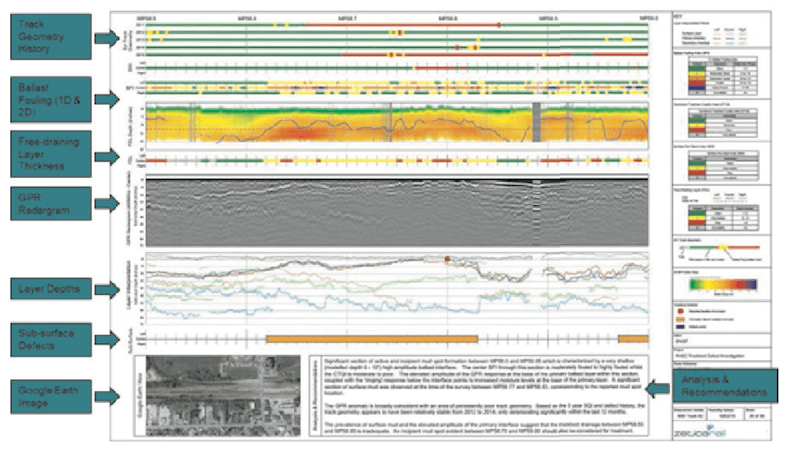
FOR ALL THE LATEST INFORMATION, NEWS, IMAGES, VIDEOS AND DOCUMENTS FROM ZETICA RAIL PLEASE CLICK HERE.