Rubber moulding is a process of creating a usable rubber product from elastomers (a natural polymer) or untreated rubber.
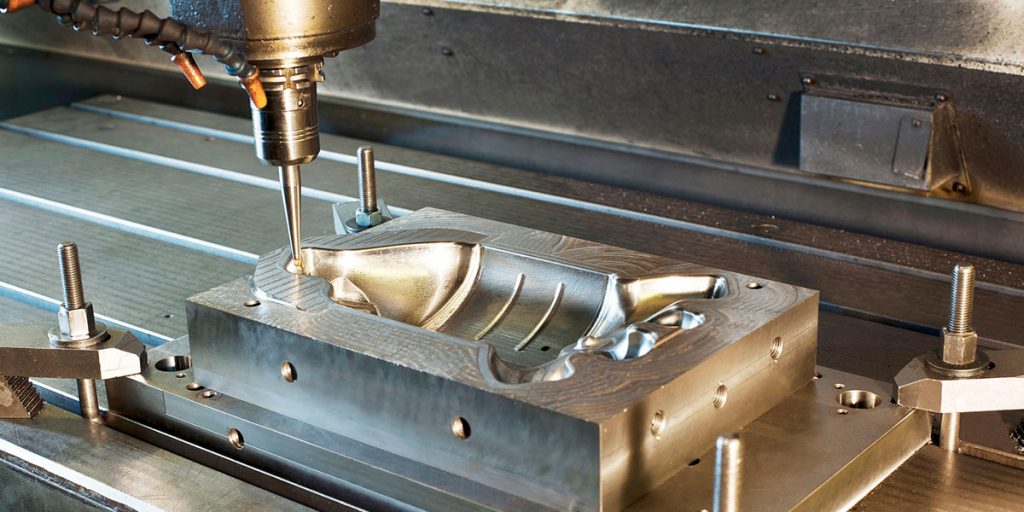
Rubber Moulding Process
Compression Moulding
It is the simplest form of moulding process in which the compound or rubber material is placed in the mould cavity directly and it takes the shape of the cavity once the mould is closed.
The uncured compound or rubber material is placed in the hot mould which is closed under hydraulic pressure. The part can be removed once the mould opens up.
The excess rubber or flash is trimmed from the part. Compression moulding is mostly done for compounds with medium hardness.
Some of the benefits of compression moulding are:
- Low tooling cost
- Best for small production
- The material doesn’t have to pass through gates, sprues or runners
Some of the disadvantages are:
- Moderate wastage of the material
- Higher labour costs
- Process time is slow
- Not suitable for complex products and tooling
Transfer Moulding
In the transfer moulding method, rather than being placed directly into the moulding cavity, the rubber compound is inserted into the tool’s transfer pot, located between the top plate of the moulding tool and a plunger. When the mould is closed, the material is compressed by the plunger, moving through sprues into the moulding cavity.
Some of the benefits of compression moulding are:
- Moderate tooling cost
- Medium to high precision parts
- Shear flow generates heat and reduces cure time
- Minimal or nil flash
Injection Moulding
It is a process in which heated rubber material or compound is injected into the mould cavity under high pressure. The material is kept inside the injection barrel. Injection moulding is the most proficient way of creating the moulded rubber products.
The uncured rubber material is fed into the injection barrel, then is warmed by an auger screw that is pulled backwards once the rubber material accumulates in front of it. Once the auger screw moves backwards, the rubber material is injected into the mould cavities by an injection press.
The auger screw is then pushed forward when the mould is closed under high pressure forcing the material into the mould cavities. The auger screw turns again to refill the injection barrel when the material is cured in the heated mould.
Some of the benefits of injection moulding are:
- Fast production
- Minimum wastage of the material
- Design flexibility
Custom Rubber Moulding Specifications
At Derby Rubber, we work with our clients to precisely determine the product that will best meet their needs.
Our range of moulded products extends anywhere from our highly abrasion resistant products supplied to mining to facilitate drilling, to intricate diaphragms that include fabric reinforcing.
Rest assured that we don’t just rely on our past achievements for continued success. Rather, we constantly look for challenges and opportunities provided by you to help us continually grow and improve our processes and techniques.
To learn more about the moulding process or our moulding capabilities, please contact us.
This article was originally published by Derby Rubber.