By Dave Walker, Parker Hannifin
Let’ s start with the basics: the four Cs challenge that has been with us for some time now.
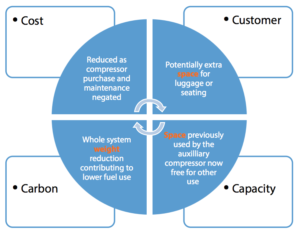
It originated from the UK Railway Technical Strategy and defines the top-level strategic drivers as:
• Cost • Customer • Carbon • Capacity
I don’t wish to go through each in detail as they are all fairly self-descriptive; however as a combined message they ask the following question: “How can we improve our CUSTOMER experience whilst increasing CAPACITY on the network, and at the same time reducing both our CARBON footprint and the COST of running the railway?”
You may ask, “how does this affect railway interiors, systems, designs and functionality, oh and by the way, what’s this diet plan you mentioned?”
Well, the four Cs are inextricably linked; for example, won’t an increase in capacity mean an increase in the carbon footprint? Won’t more capacity mean a higher cost? Or, if we take cost out, will this negatively affect the passenger experience? This is where we need to think about the relationships across the four Cs and how we, as suppliers, can think holistically to benefit the complete picture.
An example is shown above where, starting with a clean sheet, a pantograph control solution has been developed for use without the need for an auxiliary compressor.
From an interiors perspective, this example illustrates our ability to have a direct impact on the four Cs, the four key top-level drivers, particularly when we employ innovative thinking. Not all projects or activities will be able to affect all four quite so obviously. They may have a significant impact in one area whilst still having a positive impact on another, but the thought process remains.
The Diet Plan
If you look back at Fig. 1, we can see that two factors affect these four Cs and they are weight and space. These factors are also easier to address and this brings me to the diet plan:
- Weight
- Space
We at Parker have been looking at these issues for some time, wanting to improve them. It is not just a case of reducing the size of something; performance characteristics must be at the very least retained but preferably enhanced whenever possible. We also have to consider mechanical strength, suitability for the operating environment and the forces that may be applied. The reduction in size may also not result in a proportional weight loss, depending on the construction materials. Therefore, we should look at each point in isolation and then as a whole in order to achieve the ultimate end result.
Weight: there are obviously many things that can affect component weight. Size, shape and material are all key, but production method can also be vital in producing the optimum form. Just consider the ability of additive manufacturing to produce components without traditional problems, such as shape and form restraints, or material waste produced by machining. The resulting components can be complex forms that maximise material thickness; this gives us engineered solutions that are both mechanically sound yet of lighter weight, and all in a shape or form to fit and integrate into the interfaces.
Space: reducing equipment weight alone may not affect the space envelope required; however, some gains can usually be made. It is worth weighing up the cost of aiming for using less space against the cost of developing the equipment to fit. Miniaturisation in itself can be an expensive exercise. It may be better to think of the effective utilisation of available space and look at methods to reduce wasted space. As previously stated, additive (or 3D) manufacturing can go some way towards addressing this, but the optimised design must include a consideration of access for maintenance and service requirements.
However, the previously illustrated example shows: weight and space can also be reduced by returning to basics and challenging the current thinking. The “we’ve always done it this way”, or “this is best practice”, “if it ain’t broke, don’t fix it” sayings need to be challenged; then maybe a new best practice will come to light. Looking at a complete system within the vehicle along with all its interfaces from a completely clean sheet will give us the opportunity to question, review and potentially improve that system utilising the latest technology and manufacturing advances. New technologies that benefit the whole life-performance and lifecycle costs can be considered, including the IoT (Internet of Things). Operating from this level we can also take a holistic view of the vehicle system with the four Cs in mind. The link, then, to innovation – which may not mean a completely new solution, but could include technology transfer from other industries and utilising alternative technologies – can truly be explored and the benefits maximised.
To discuss how Parker can help you address the 4 Cs utilising a holistic system design approach please contact Dave Walker, Parker’s Rail Market Development Manager at [email protected].
FOR ALL THE LATEST INFORMATION, NEWS, IMAGES, VIDEOS AND DOCUMENTS FROM PARKER, PLEASE CLICK HERE.