Replacing traditional maintenance regimes with condition-based monitoring will help rail operators to reduce the time they spend servicing their rolling stock, write SKF’s Nils Ekholm and Mark Rhodes (Nils Ekholm is a Technical Leader for the new market offer at SKF, while Mark Rhodes Technical Leader for the development project at the company).
Condition-Based Monitoring
The rail industry’s prevailing maintenance regime is to service trains on a time or mileage basis. Though it has been used successfully for many years, it does not take account of whether parts actually need replacing. Nor is it effective at preventing breakdowns.
Condition-based monitoring (CBM), which measures parameters such as vibration and temperature to spot anomalies at an early stage, has been commonly applied for a long time in many industries. However, the railway sector has been slow to adopt it – due in part to a number of safety regulations that govern it but also to that suitable technology has not been available. Recently, though, a number of other industry drivers have come to the fore that could see CBM being adopted more widely in the rail sector.
Identify Rolling Stock Problems Early
The main factor is efficiency. Rail schedules are crowded, and tracks are more congested. Rail operators are under pressure to work as efficiently as possible and keep their rolling stock in good working order. Trains need to be out on the track – ferrying passengers around – rather than spending long periods of time in maintenance depots, being serviced.
But if maintenance is a drag on resources, disruptions, caused by breakdowns, are even worse. So in addition to cutting maintenance time, rail operators must minimise the breakdowns that cause so much misery for commuters.
CBM can help achieve this in two main ways: it identifies problems early, which reduces the risk of breakdowns; and, it can reveal when ‘old’ parts are perfectly healthy – which, in turn, helps to extend maintenance intervals and keep them out of the depot for as long as possible. The technology is well proven within the manufacturing sector, and companies such as SKF have applied it to the rail industry with a high level of success.
Wireless CBM System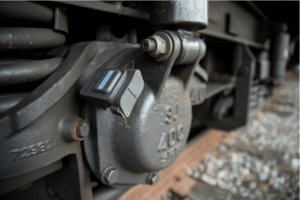
SKF has actually gone a step further, by developing a wireless CBM system – called SKF Insight – that can be used on trains. It consists of retrofitting a small sensor onto the wheelset axlebox assembly of the train, to detect bearing damages.
The sensor picks up tiny inconsistencies in the vibration of a bearing as it begins to fail – despite it being in an environment wracked by noise and other vibrations. Sophisticated signal processing and algorithms separate the signal from the noise, ensuring that each sensor produces accurate data for further analysis.
Each of the wireless sensor nodes has an array of different sensors included and is capable of taking several different measurements pertaining to bearing health including SKF Acceleration Enveloping (gE), and temperature. The sensor node is provisioned with GPS for location and speed; three-axis accelerometer; movement sensor; a temperature sensor; high sensitivity and high-frequency vibration sensor; real time clock. Each sensor node can be remotely configured to meet individual customer’s specific monitoring needs and operating schedule. An integrated battery avoids the need for external cabling and offers a reliable, predictable, long-lasting source of power.
Detecting Bearing Health
SKF Acceleration Enveloping (gE) is a long established vibration measurement which is proven to give early indications of bearing damage. A standard acceleration vibration measurement is band-pass filtered rectified and finally enveloped. Advanced processing and trending of the resulting signal are then performed using the software SKF @ptitude Observer. Using this measurement it is possible not just to detect the presence of damage but also to determine what bearing component is damaged (i.e. rollers, cage, outer raceway, inner raceway). For vibration activity to be classed as symptomatic of bearing damage periodic activity must be consistently present in the data at sufficient magnitude and at very specific frequencies.
Temperature measurements typically give a significantly later indication of bearing damage than gE with sudden and sustained increases in temperature indicative of a possible imminent failure. The inclusion of the temperature data is intended as complimentary to the vibration data (gE) which forms the core of this analysis.
The whole system uses wireless reporting. The sensor’s data is sent to a remote diagnostics centre, using mobile data. There is no need to fit a cumbersome onboard router, and all the cables have been removed.
Having been used in the proof of concept system, the sensor technology itself is well proven. It can be installed in a few minutes, by fitting on one of the bolts that screw the axlebox cover into place.
As well as detecting bearing health, the system also monitors wheel flats. These are usually caused during braking and – if left unchecked – can damage the track. Ordinarily, wheel flats are monitored using track-side detectors, but SKF Insight can also perform this vital operation.
Reducing Data Collection Time and False Alarms
Collecting and sending the data is one thing – but acting on it is something else. Rail operators do not want to plough through mountains of data and interpret it. Instead, they want clear recommendations for action. So, once the data has been processed and analysed it is used to produce a simple report.
An automatic alarm will trigger whether an action is needed. SKF experts then check the output and produce a report – such as recommending a planned replacement of the bearing.
SKF has worked to reduce the amount of data to the customer – and the number of false alarms. As well as bearing data, the system analyses information on temperature – as well as speed and positional data using GPS. All the generated data is stored in the SKF Cloud.
The system is moving out of the development phase, following a successful field trial: during 2015, the system was fitted to a railway vehicle owned by the Swedish national railway operator, SJ, and accurately diagnosed three damaged bearings. Next, it will go through verification and validation in early 2017, when it will be fitted to more trains in the field. The full system is due to be launched first half of 2017.
Original article © SKF.
FOR ALL THE LATEST INFORMATION, NEWS, IMAGES, VIDEOS AND DOCUMENTS FROM SKF, PLEASE CLICK HERE.